For over 4 years, more than 150 Staticus employees have been working on an exceptional Hospital project – the New North Zealand Hospital (Nyt Hospital Nordsjælland) in Denmark. The vast and complex façade for this huge scale hospital features a nature-inspired design by Herzog & de Meuron and Vilhelm Lauritzen Arkitekter.
In this case study, key members of the Staticus team – Project Manager Jonas Garbaliauskas, Project Engineers Paulius Rapkevičius and Lech Stankevič, Concept Design Engineer Tommaso Martimucci – share their insights on the unique requirements of this hospital façade, and how we have found smart solutions to meet them.
A new huge scale hospital
New North Zealand Hospital will be one of the most significant Denmark’s hospitals. Located in Hillerød, 35km north of Copenhagen, it will be home to 20 medical departments that employ around 4,000 staff and serve more than 300,000 citizens. This 124,000 m2 facility will include 570 patient rooms.
The 4-storey hospital building, commissioned by NCC DK for the Capital Region of Denmark, stands in strong contrast to traditional hospital designs. It features a unique “clover-leaf” shape and a shared garden in the centre. The lower 2 floors are home to treatment areas, while the upper 2 floors comprise a ribbon of wards.
The façade project at a glance
- Location: Hillerød, Denmark
- General Contractor: NCC DK
- Architects: Herzog & de Meuron and Vilhelm Lauritzen Architects
- Building area: 124,000 m2
- Facade area: 20,000 m2
- Type of construction: New construction
- Investor: Capital Region of Denmark
Staticus is tasked with delivering the engineering, production, and installation of the main building envelope for North Zealand Hospital. We are responsible for façade type A, which covers the almost 1km perimeter, and façade type D, which is used for the bed ward façade. We are also handling the skylights and metal roof, which we are delivering together with local partners in Denmark.
In total, we are producing and installing 20,000 m2. This equates to approximately 2,020 aluminium-glass double-height (two storey) façade elements. Over 150 team members have been involved in delivering this project, which was our largest ever at the time of contracting. It is also our first project in Denmark.
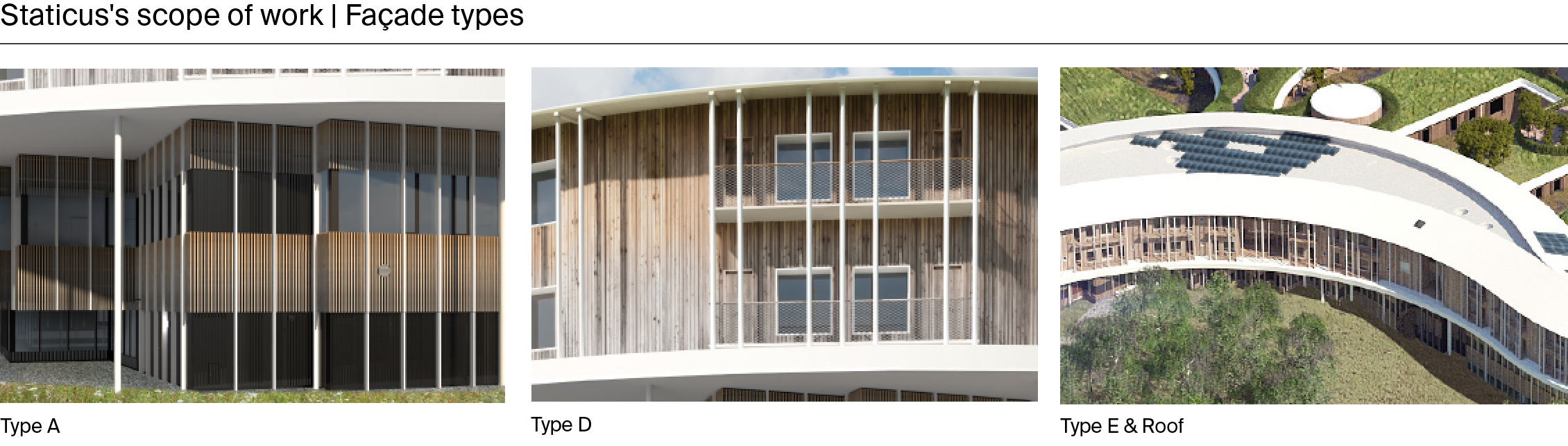
A spectacular architectural vision connecting patients to nature
New North Zealand Hospital has been designed by Herzog & de Meuron and Vilhelm Lauritzen Architects, who won an international competition for this project. Their design throws out standard practices in hospital design in favour of a bold and patient-oriented vision. “From the architectural side, this is a very complex but very interesting building,” comments Jonas Garbaliauskas, Staticus’ Project Manager for this project.
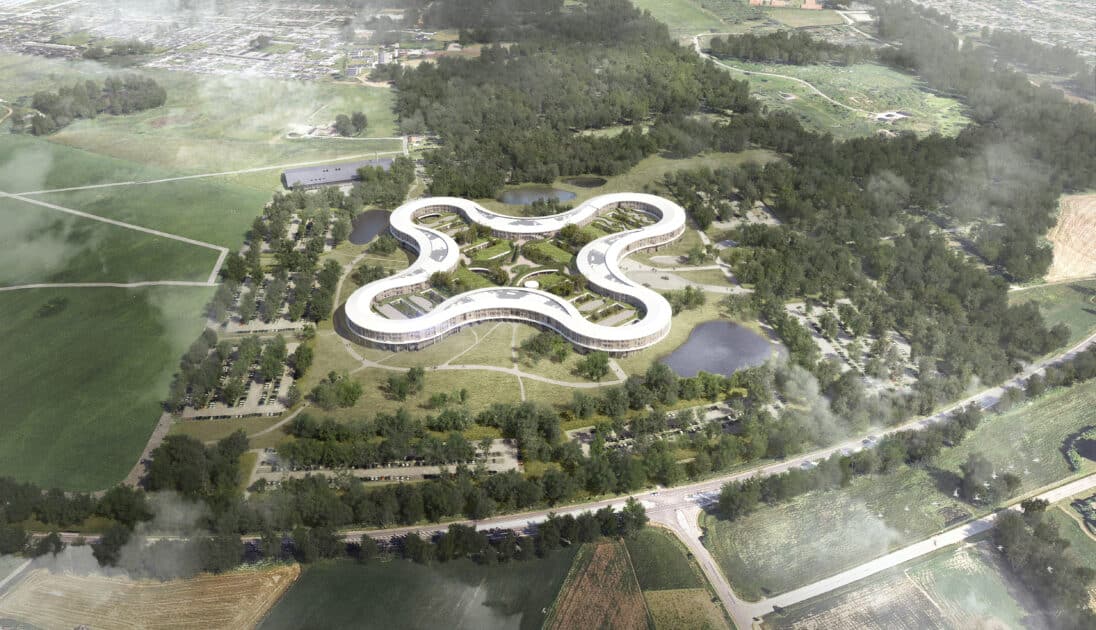
The building’s low-rise “clover leaf” design balances two contrasting needs – giving patients views of nature and access to a central garden, while at the same time ensuring short internal connections within the hospital that foster exchange between departments.
The curved perimeter – which forms a large garden in the centre – features elegant geometry that reduces the size of the hospital and gives it a more human scale.
This design meant increased complexity in terms of the façade, as Jonas explains. “We frequently work on high-rises, and these buildings typically have unique elements on the ground and top floors. Meanwhile, the remaining floors are more or less repeated. With North Zealand Hospital, which is a low-rise, widely spaced building, every floor is different and complex.”
Connecting patients to nature
A central tenet of the architectural vision is a direct and meaningful connection to nature, which is achieved in three ways.
Firstly, the design itself responds to the rural landscape. “The building design has slopes and a variety of different heights,” comments Jonas. “The surrounding scenery is reflected in the façade design, and we have had to follow the landscape’s line and altitude.”
Secondly, there is the greenery of the building itself. The design features a large central roof garden.
Thirdly, the design enables patients to directly connect with the natural beauty surrounding the hospital. The upper floor wards look either outward, into the Danish landscape, or inward, into the central garden. “To enhance this connection with nature, the building envelope is designed to blur the boundaries between interior and exterior,” explains Jonas.
Incorporating wood into the façade
To further strengthen the connection with nature, and provide patients and staff with a comforting and warm built environment, the architects chose to make timber a key feature of the hospital’s façade.
At Staticus, we have an extensive track record working with timber thanks to our long history in the Nordics, where this material is especially popular. “In Norway and Sweden, where we have worked for many years, wood is valued for its aesthetic and thermal properties, and its sustainability benefits,” Project Engineer Paulius Rapkevičius points out. We have built up extensive know-how working with this material. We have developed our own timber-based hybrid unitised façade as part of a project funded by the 2014-2021 Norwegian Financial Mechanism Program “Business Development, Innovation and SMEs” EEA and Norway Grants. And we continue to work with research partners on innovative ways to incorporate timber into façades.”
“The New North Zealand Hospital adds another outstanding timber envelope project to our portfolio.”
Over 14,000 m2 of timber used
“We used approximately 14,000m2 of wooden material for this façade,” Paulius continues. “For type A, we employed vertically-oriented open-joint cladding elements. For the type D façade, wood lap sidings were used. The challenge was to achieve a seamless effect when approximately 80% of the elements had different layouts for the boards.”
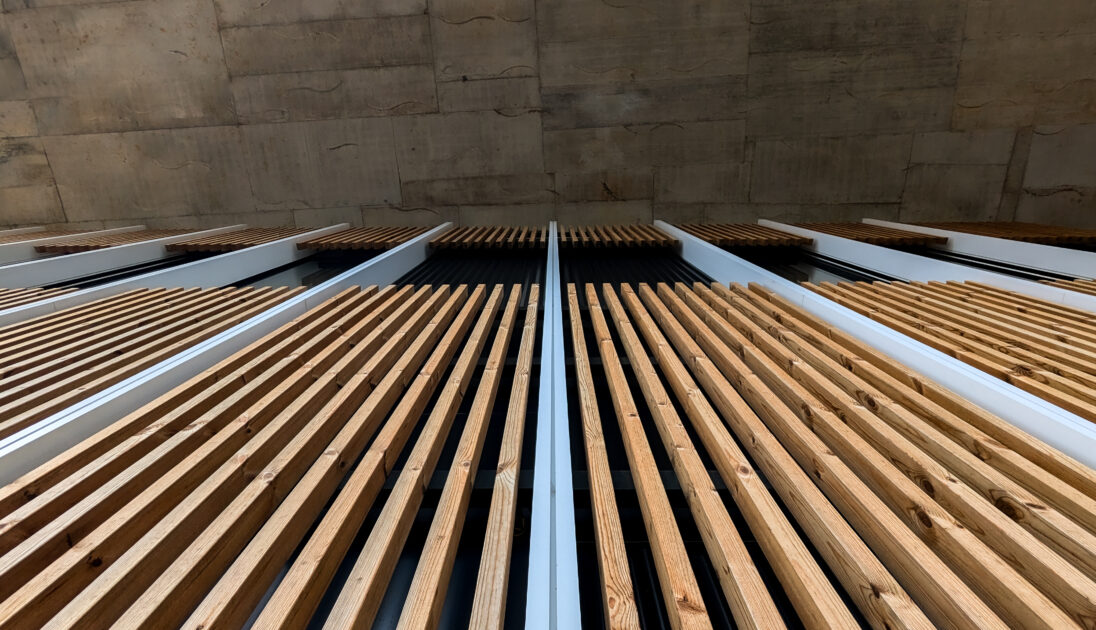
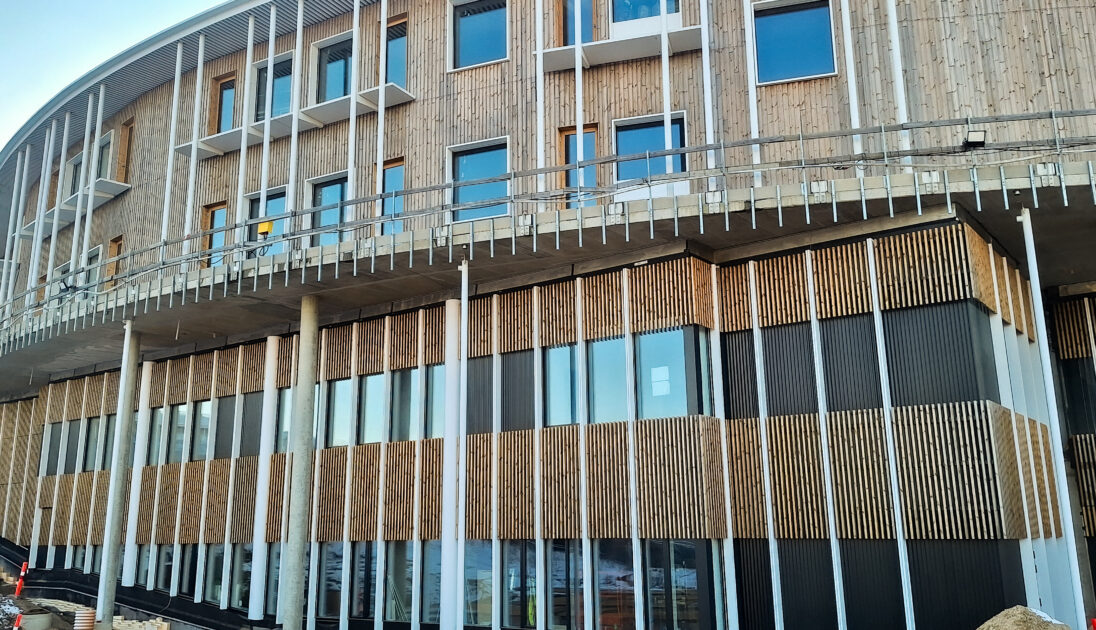
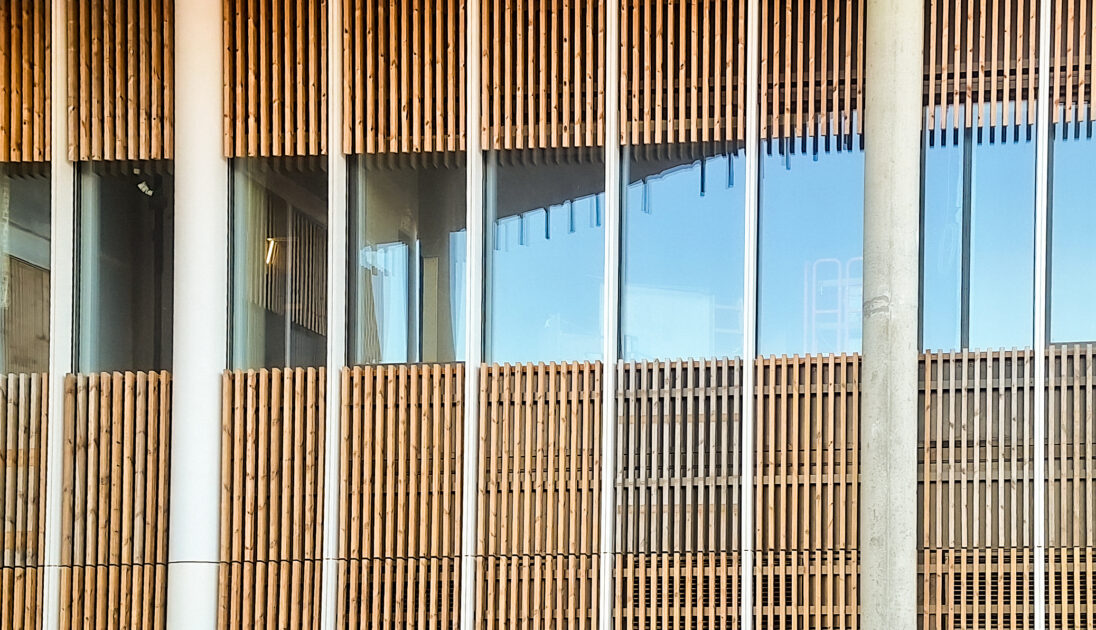
Heat-treated timber
Thermowood D pine was selected for this project. This is a heat-treated thermo pine that is produced in Denmark and carries the Nordic Swan Ecolabel.
“The thermal treating is designed to kill any organisms and dry out the wood as much as possible,” says Paulius. “This makes it stable. The idea is that none of its properties will change over time, except for its colour, which will gradually become more grey over time.”
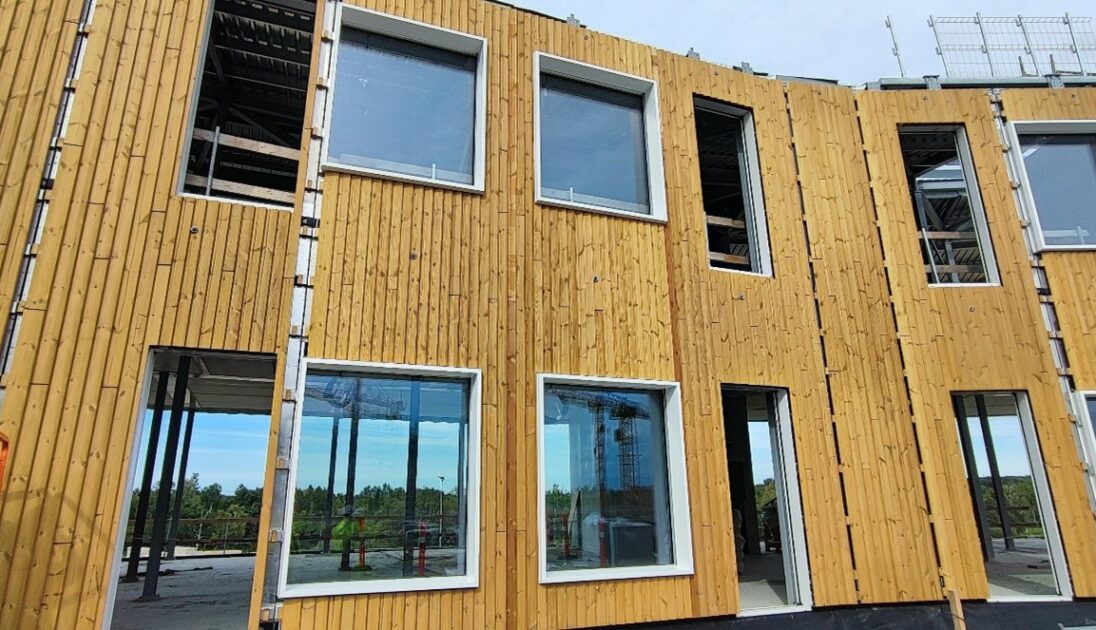
Patient comfort and well-being
Along with its major contribution to the hospital’s aesthetic vision, the façade also plays a key role in ensuring patients enjoy optimal conditions for recovery and healing.
“Hospital buildings are not like offices,” explains Project Engineer Lech Stankevic. “There is a much wider variety of different rooms and workspaces, each with unique specifications and requirements. The building envelope for this project needs to enable staff and patients to connect with the surrounding nature, while also maintaining a comfortable interior and meeting high performance requirements.”
Acoustic requirements
Good sound insulation creates a quiet, peaceful environment in which to recover, and ensures patient privacy as well.
As a result, the acoustic requirements for the New North Zealand Hospital façade were high, especially for the horizontal and vertical flanking on the type A façade. The required level was 55 dB Dnfw horizontally and 54 dB Dnfw vertically. “In some cases, the requirement for the vertical flanking was as high as 63 dB,” adds Jonas. To achieve this acoustic insulation, the mullion voids were filled with high performance acoustic materials at the wall and floor intersections as well as horizontal divisions of units between floors were added.
A complex, large-scale project
We have been involved in the North Zealand Hospital project from the design development stage onwards. “The team working at the pre-tender stage was probably the largest we have ever dedicated to a project,” comments Jonas. “A lot of our best minds have worked with enthusiasm and dedication to find solutions for the multiple requirements of this project.”
The project’s scale is matched by its complexity. “The two-storey façade for the ground level is set back from the floors above and includes staggered corners to follow the curve of the building,” adds Paulius. “The upper levels also follow these curves, and therefore accommodate multiple radii in the connections. As a result of this complexity, more than one quarter of the elements are unique. In total, we have produced and installed 566 different façade element types.”
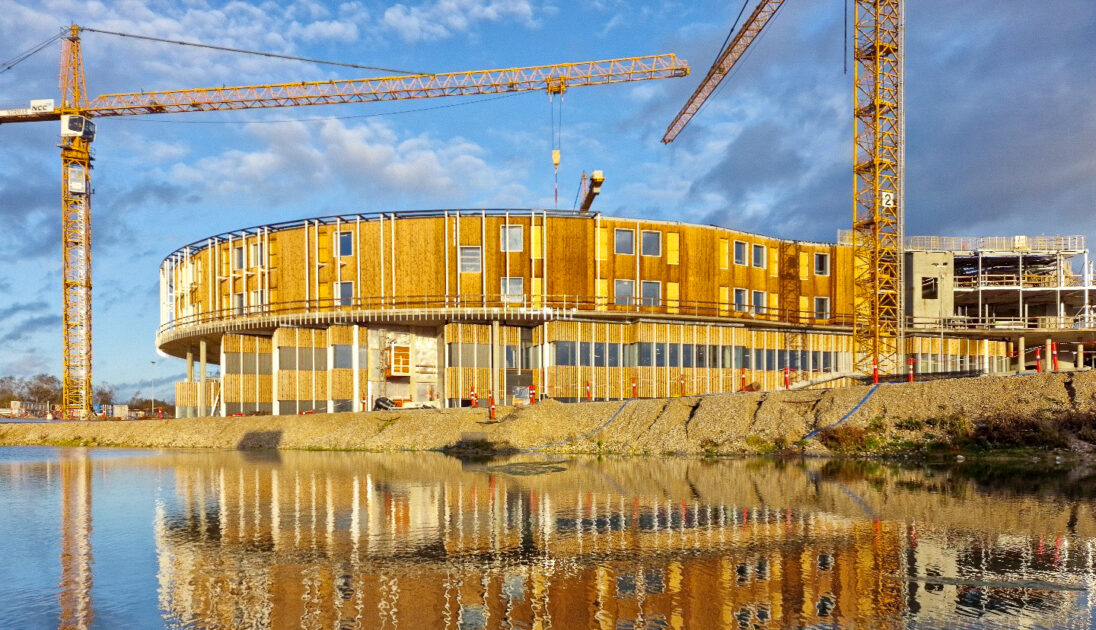
Turning vision into reality
Realising such an ambitious architectural vision, at such a large scale, and with so much complexity, has required a huge effort from the Staticus team.
“The statistics on our working hours for this project are mind-blowing,” says Jonas. “We invested three times more hours than average in design, production and installation as well, reflecting the scale and complexity of this project.”
“Our general performance on this project has been outstanding, especially given the enormous scale,” Jonas continues. “We have been able to meet all of our project milestones on time, working in close collaboration with the NCC DK and the architects.”
A precisely calibrated value chain
This strong performance has only been possible thanks to excellent coordination across the various stages of our project.
“In general, our specialisation with unitised prefabrication has played a huge part in the successful delivery of this project,” Jonas explains. “The majority of structures have been delivered to the construction site having been preproduced, and the design team has played an important role in enabling efficient installation. The units were designed to span over two floors, which brought efficiencies, but also meant they were very tall – the Type A units are up to 8.3 metres tall, and the Type D units reach 7 metres. “
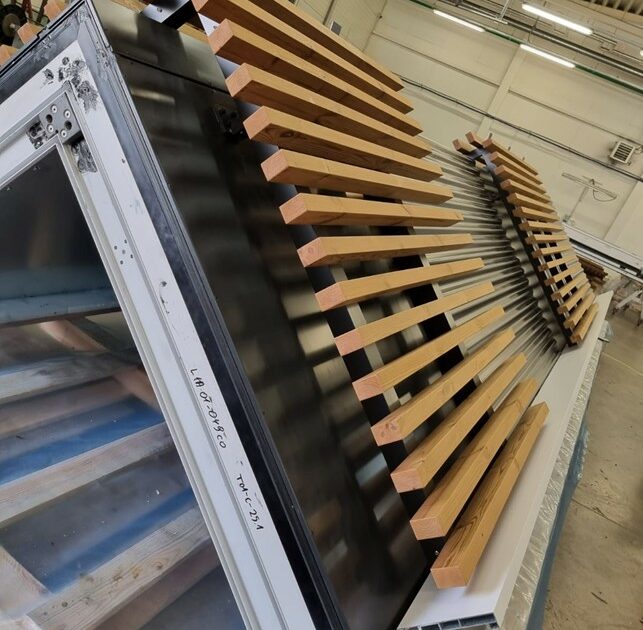
“This height has brought installation challenges. We have used robotic forklifts to accurately place the units on site. Then for the upper-floor Type D elements, we have used a tower crane to lift the elements safely and efficiently from the preparation to the installation zone.”
At over 123,000 m2, the site is one of the largest construction sites in Denmark. Therefore, careful coordination of work with other contractors and precise logistics have been essential. By testing the installation process prior to going on site, and then continuously increasing efficiency once installation began, the team has been able to optimise this stage of the project.
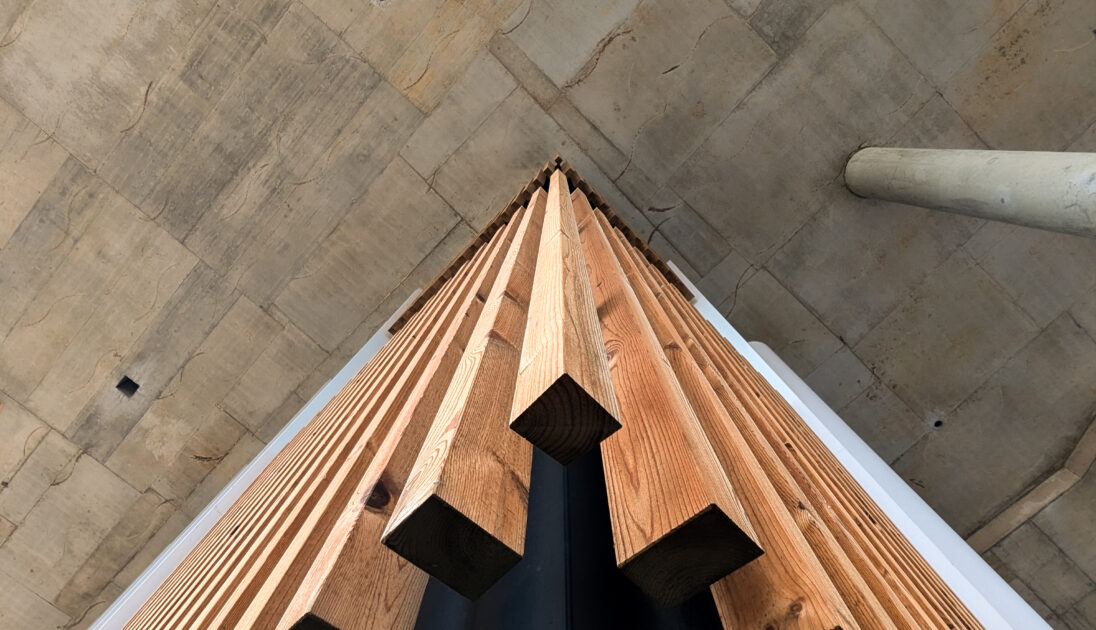
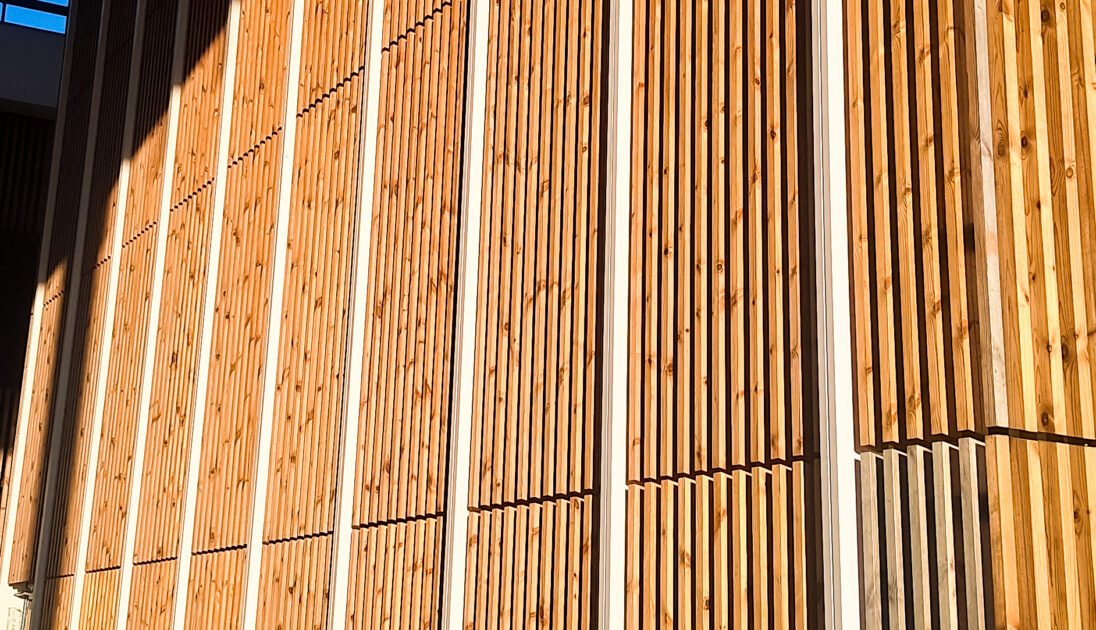
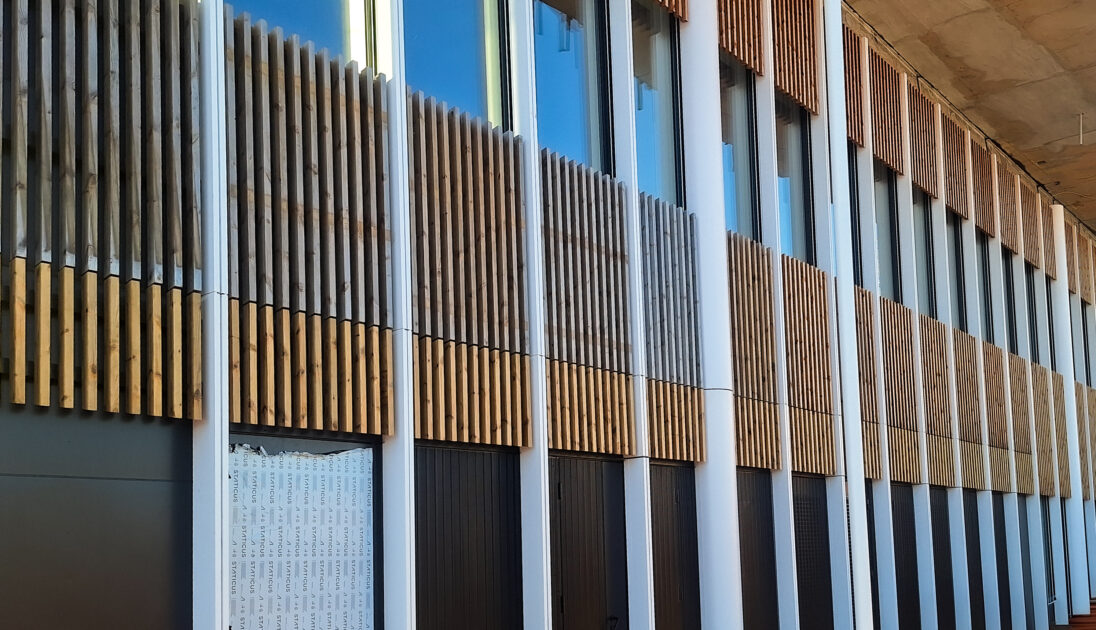
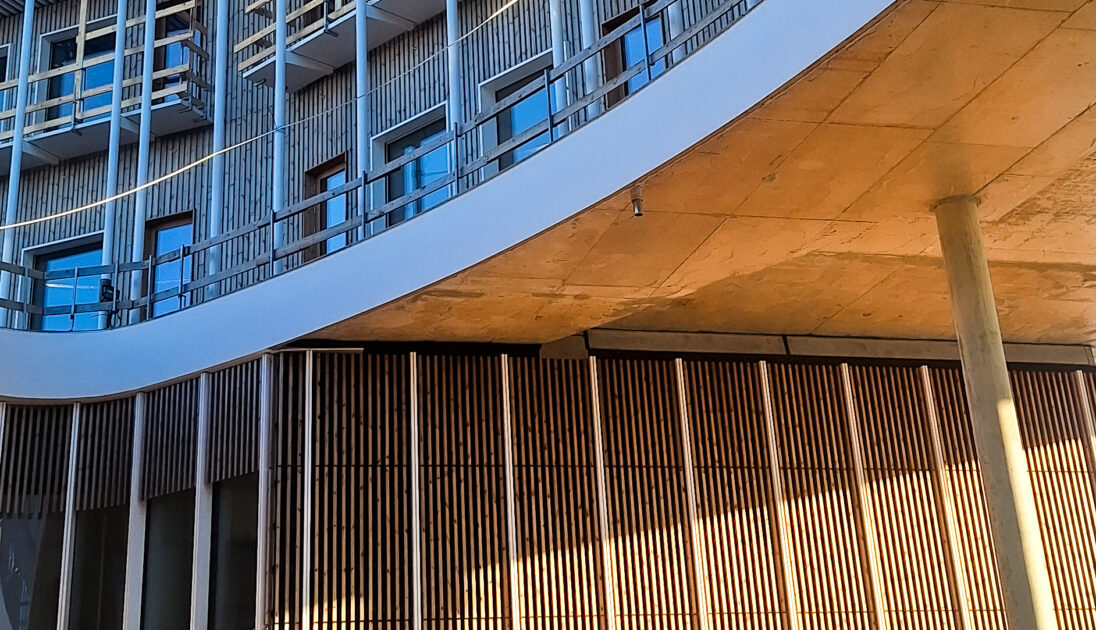
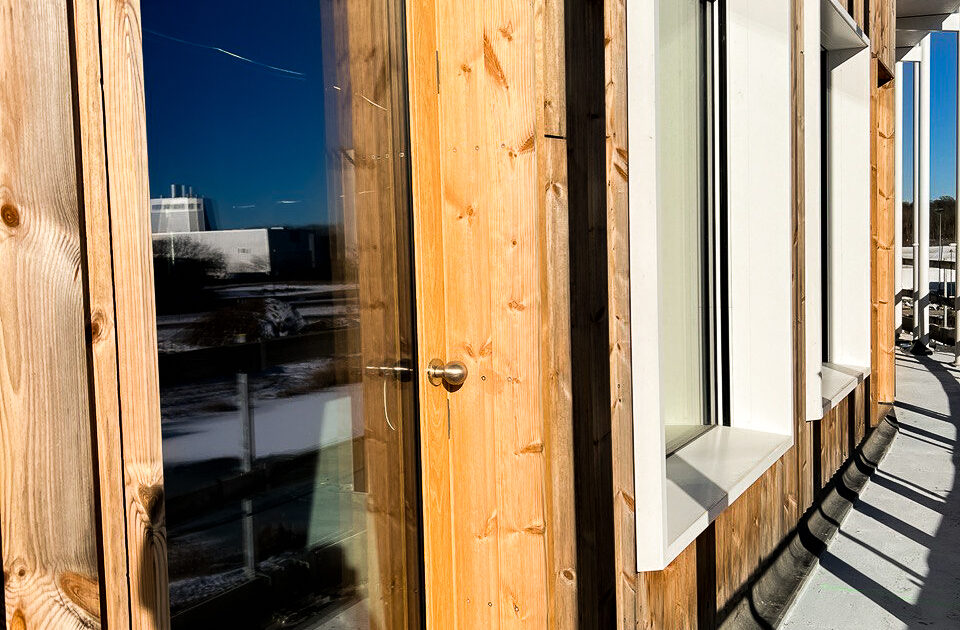