Pilefaçade is an interdisciplinary research and development project exploring how a fast-growing, locally sourced plant – willow – can be transformed into a scalable, prefabricated façade system. Combining biogenic material innovation with industrial manufacturing precision, the project charts a path toward low-carbon construction through regenerative design.
The project was initiated following its selection as one of just four recipients of Denmark’s Implement Materials grant – a national initiative supporting innovative approaches to materials in architecture. This recognition provided the foundation for an ambitious collaboration between Staticus, Schmidt Hammer Lassen Architects, PILEBYG A/S (a Danish willow grower), and MOOW – Made Out of Willow, with a shared vision to bring willow into the realm of high-performance façade systems.
A vision for sustainable architecture at scale
Biogenic materials have long held promise for sustainable construction, yet their use remains limited to small-scale or experimental projects. Pilefaçade challenges this status quo. The project investigates how willow, a fast-growing, high-CO₂-sequestering perennial, can be integrated into large-scale unitised façade systems as functional, structural, and aesthetic material.
The system reimagines how buildings are clad and insulated by incorporating multiple willow-derived components:
- Laminated structural frames from thick willow trunks
- Pressed boards from bark and offcuts
- Rainscreen cladding from slender, natural-form willow branches
- Potential future applications: insulation, acoustic panels, and internal finish layers
By rethinking the role of plant-based materials in prefabricated assemblies, Pilefaçade offers a viable alternative to carbon-intensive materials like aluminum, steel, and conventional timber.
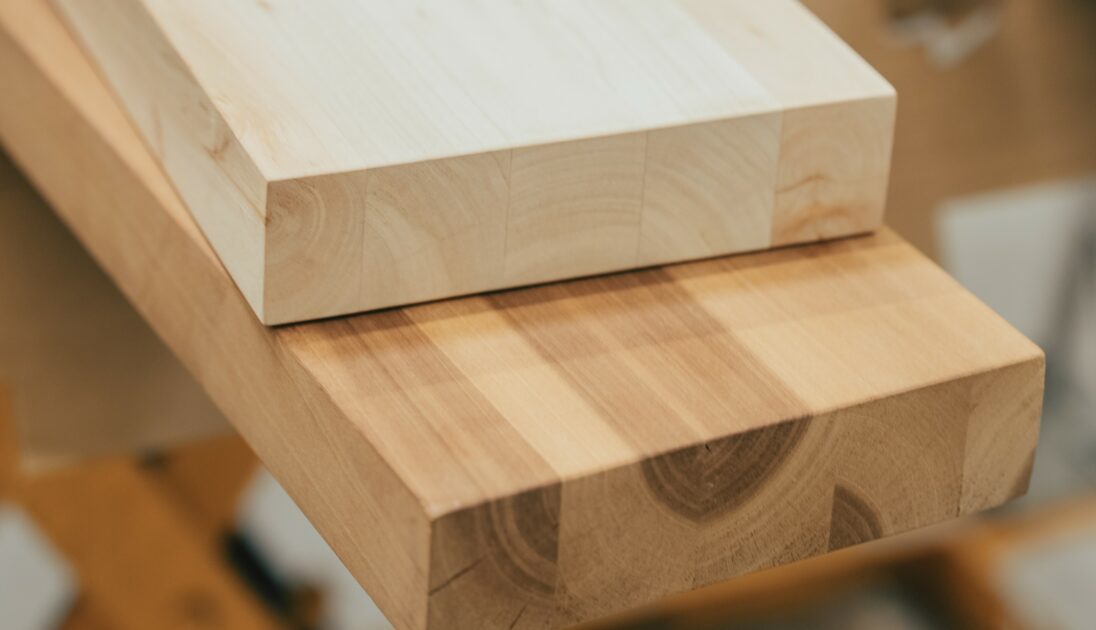
From plant to panel: A regenerative material strategy
Willow (pil in Danish) is uniquely suited for architectural application. Grown as a perennial crop in Northern Europe, it regenerates after harvest without the need for replanting, fertilizers, or irrigation. It absorbs 10–15 tons of CO₂ per hectare annually, and with rotation cycles of just 4–8 years, it is among the most rapidly renewable biomass resources available.
The Pilefaçade project takes a full-plant approach, utilizing each part of the willow tree:
- Thick branches form laminated load-bearing elements
- Residual material becomes compressed board
- Slender branches are used in rainscreen cladding, left in their natural form to preserve both texture and protective qualities
This strategy minimises waste and maximizes carbon storage, with prototype calculations suggesting the potential to reduce embodied carbon by over 50%, or up to 150 kg CO₂e/m² façade surface area.
Project collaboration
Pilefaçade’s innovation is not only material-based but systemic. It links farming, design, and manufacturing in a fully integrated value chain:
- PILEBYG A/S – Cultivation and harvesting of willow
- MOOW (Made Out of Willow) – Material transformation and processing
- SHL Architects – Architectural design and façade integration
- Staticus – Prefabrication, production engineering, and prototype delivery
At Staticus, the project was initiated and nurtured by Laura Craft, Head of Sustainability, and Aulikki Sonntag, Chief Business Development Officer. Their early leadership helped steer the company toward deeper exploration of biobased materials. As interest grew, our Senior Concept Design Engineer Audrius Buslevičius and Head of Sustainability, Laura Craft, traveled to Denmark to visit PILEBYG’s plantations – observing firsthand the growth, harvesting, and thermal treatment of willow.
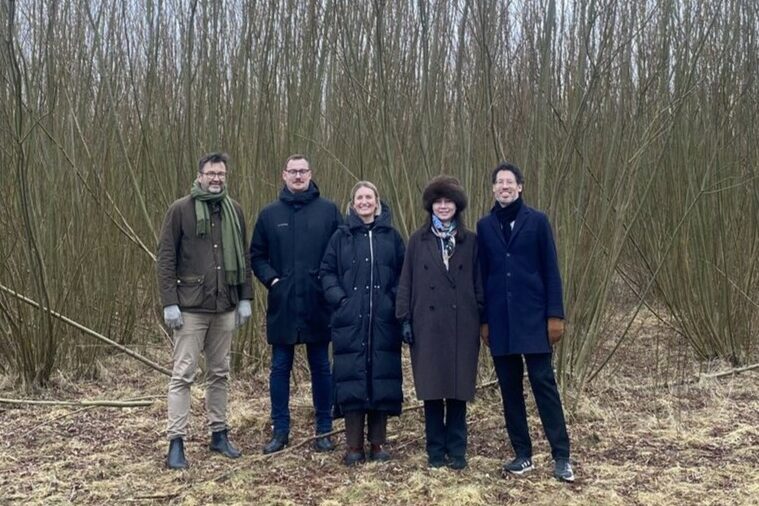
The team explored the production of cladding elements, studying techniques like lamination, gluing, drying, and shaping. A key insight was willow’s ability to regrow from cut stumps without the need for fertilizer or irrigation, absorbing moisture directly from the soil and supporting biodiversity through its non-invasive, regenerative cycle.
Designed for performance and circularity
The system is based on unitised curtain wall logic, integrating preassembled modules that reduce on-site construction time and enhance quality control. Among the four design options explored, the selected solution emphasizes natural bark-finished cladding for tactile texture and natural weather resistance.
Key design features:
- Click-in mounting system – Concealed for seamless aesthetics, removable for maintenance and reuse
- Modular structure – Engineered for rapid assembly and circular disassembly
- Precision fabrication – CNC-processed despite the irregularities of a natural material
Performance tests have already shown promising results. Moisture, density, and drilling tests conducted at DTI and Aalborg University confirmed structural integrity, while fire and acoustic evaluations are ongoing through DBI and SWECO. The system is now progressing toward Environmental Product Declaration (EPD) certification and CE-marking.
Public debut and industry dialogue
The Pilefaçade system has been presented across key industry platforms, engaging architects, engineers, and developers in real-world conversation about next-generation façades:
- April 10, 2025 – Implement Materials Exhibition, Frederiksberg Hospital, Copenhagen
First public debut of the mock-up; Staticus presented its pre-manufactured design approach. - May 7–8, 2025 – Future Facade Conference, Utrecht, Netherlands
Featured in the Maze of Innovations. Laura Craft and Aulikki Sonntag joined the speaker program with the willow mock-up. - May 23, 2025 – Team Talk at Implement Materials, Copenhagen
The full Pilefaçade team discussed technical, ecological, and strategic development with the public. - June 18–20, 2025 – DDcated at 3 Days of Design, Copenhagen
The mock-up was exhibited among Denmark’s leading design companies, showcasing the merging of nature and innovation - September 11, 2025 – Performance-Based Façade Design (PBFD) Conference, Copenhagen Laura Craft will present “Smart Technology and Biobased Innovation in Next-generation Timber Façades”, discussing the evolution of Staticus’ hybrid systems and new insights from the willow-based prototype.
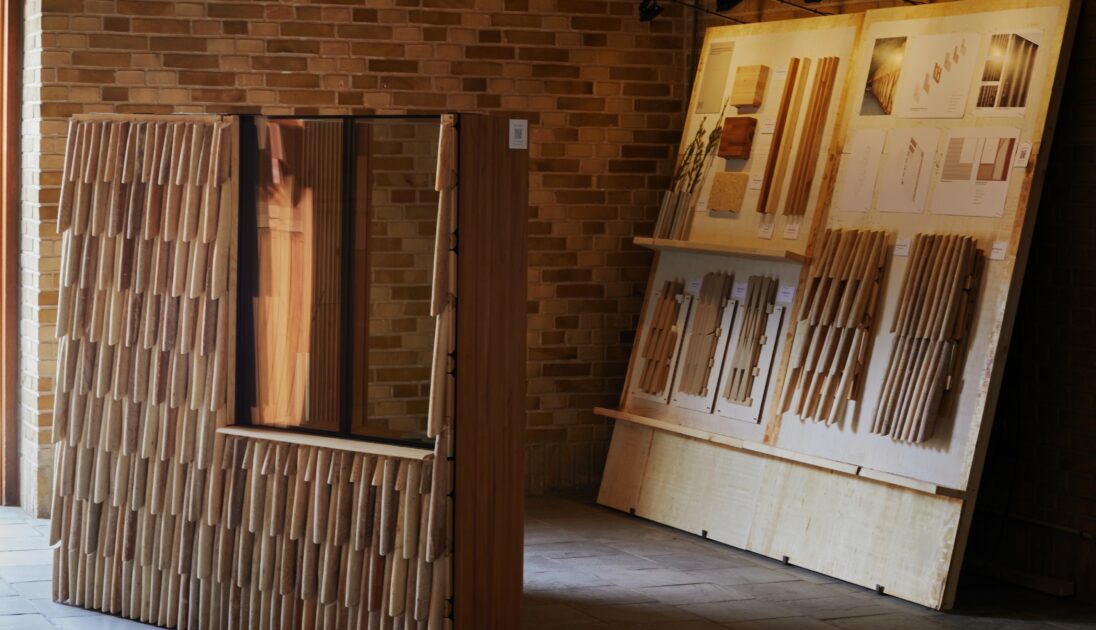
Next steps: Toward real-world implementation
Pilefaçade is currently transitioning from TRL 5 (validated in relevant environment) toward TRL 8 (real-world demonstration). Key development priorities include:
- Full-scale fire, moisture, and wind-resistance testing
- Optimization of lamination, drying, and thermal processing
- Establishment of a consistent supply chain from plantation to prefabrication
- Pilot implementation in architectural projects
- Exploration of façade-as-a-service business models
A façade that grows with purpose
Pilefaçade is more than a material experiment – it is a model for ecologically integrated architecture, where natural growth cycles, digital design, and industrial production meet in service of the built environment. As cities move toward circularity and decarbonization, projects like this point the way forward: facades that are grown, not extracted; assembled, not wasted; and designed for both performance and planet.
Project team
Staticus, PILEBYG A/S, MOOW – Made Out of Willow, SHL Architects. Supported by Arkitektforeningen and Dreyers Fond.