The Via Vika building in Oslo, Norway, is a ground-breaking project for many reasons. It is the first ever building in Northern and Eastern Europe to feature a closed cavity façade (CCF). It also combines two different types of façade – CCF and single skin (SSF). Then there is the sheer scale of the project – the 20 000 m² office and retail complex features over 2,000 façade units.
Staticus designed, manufactured and installed the façade for the Via Vika project, using ingenuity, teamwork and expertise to overcome challenges at every stage. These included:
- Designing and installing a solution that featured different types of both façade – closed cavity and single skin,
- Working with complex materials including patterned stainless steel coated in Rosy Gold via a deposition process, and natural limestone,
- Realising a bold architectural vision that included two separate buildings and a skylight 12m in diameter,
- Creating completely new production facilities in order to produce CCF façade elements using Dry Air technology for the first time ever,
- Undertaking the company’s largest ever façade installation, which was interrupted by quarantines due to the COVID-19 pandemic.
In this case study we will look behind the scenes at how the Staticus team completed this ambitious and complex project.
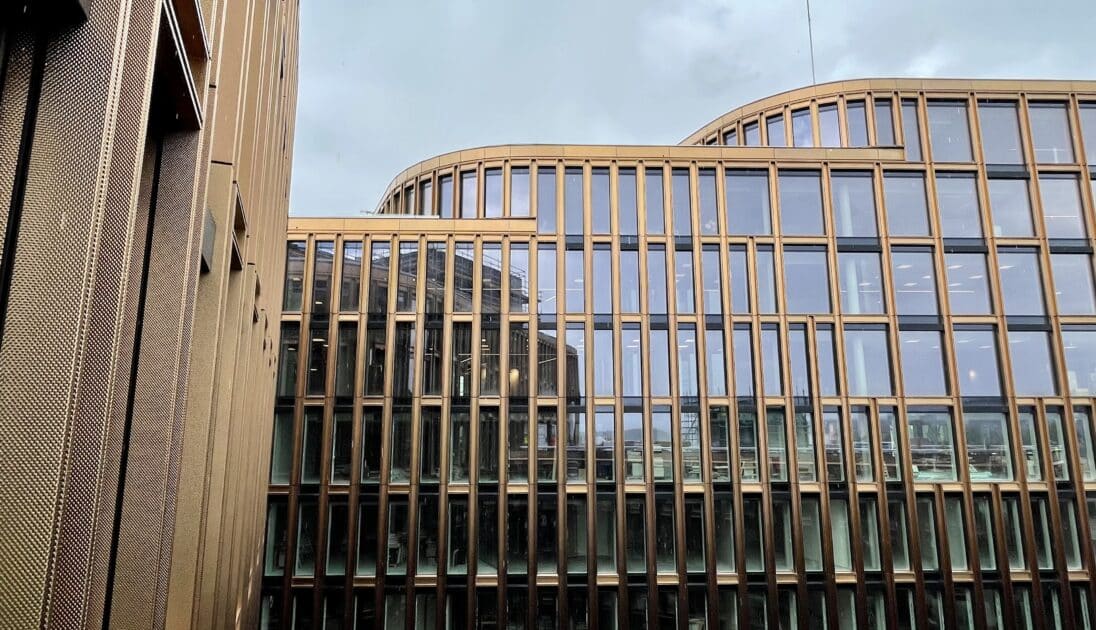
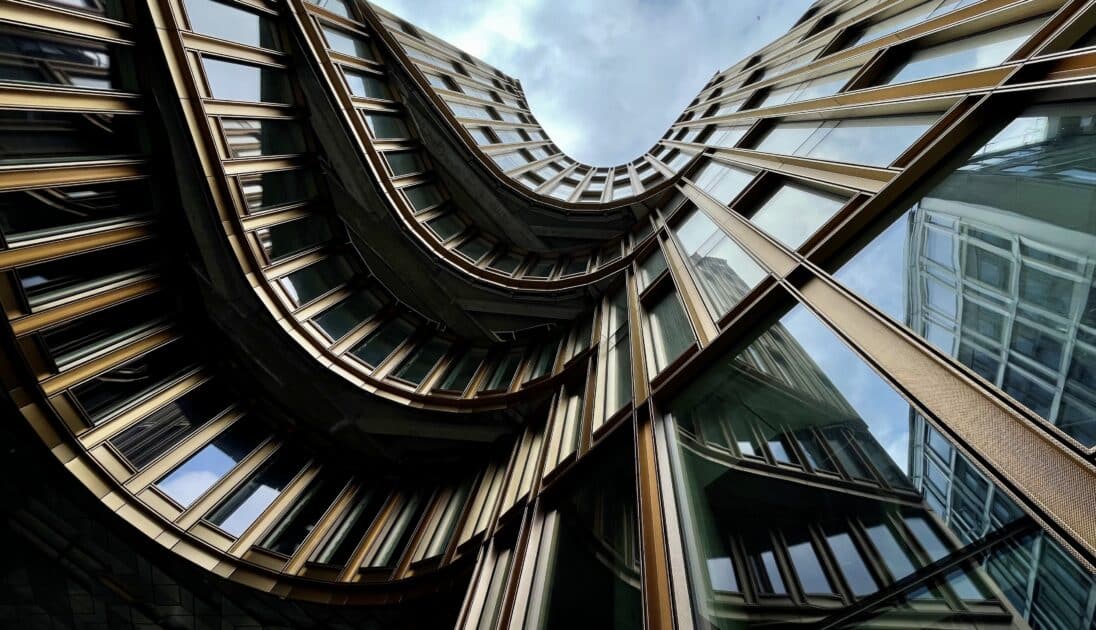
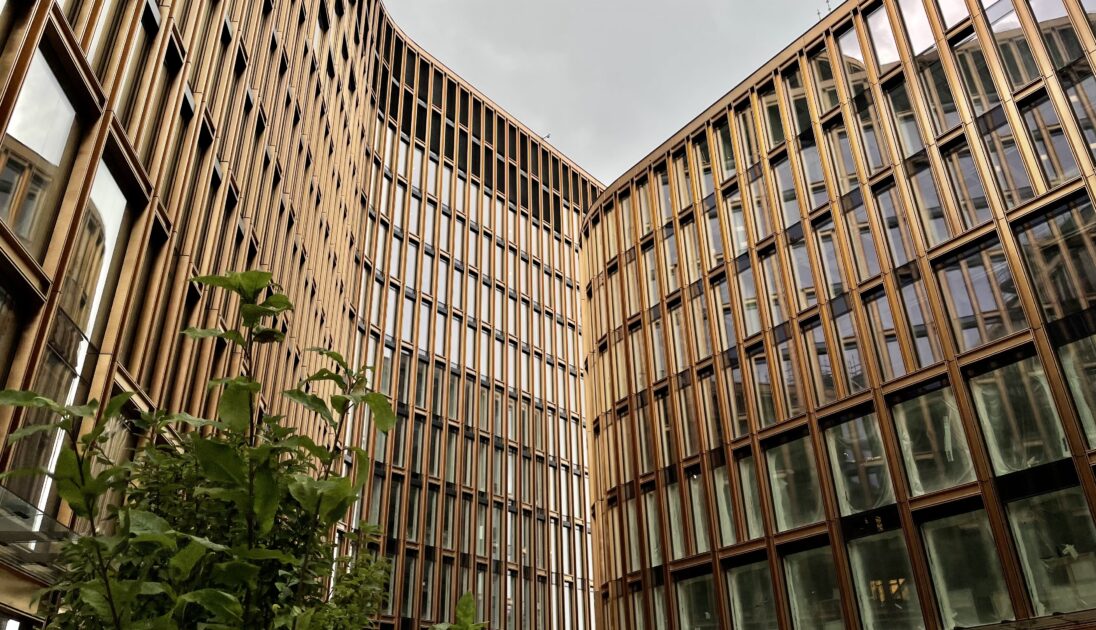
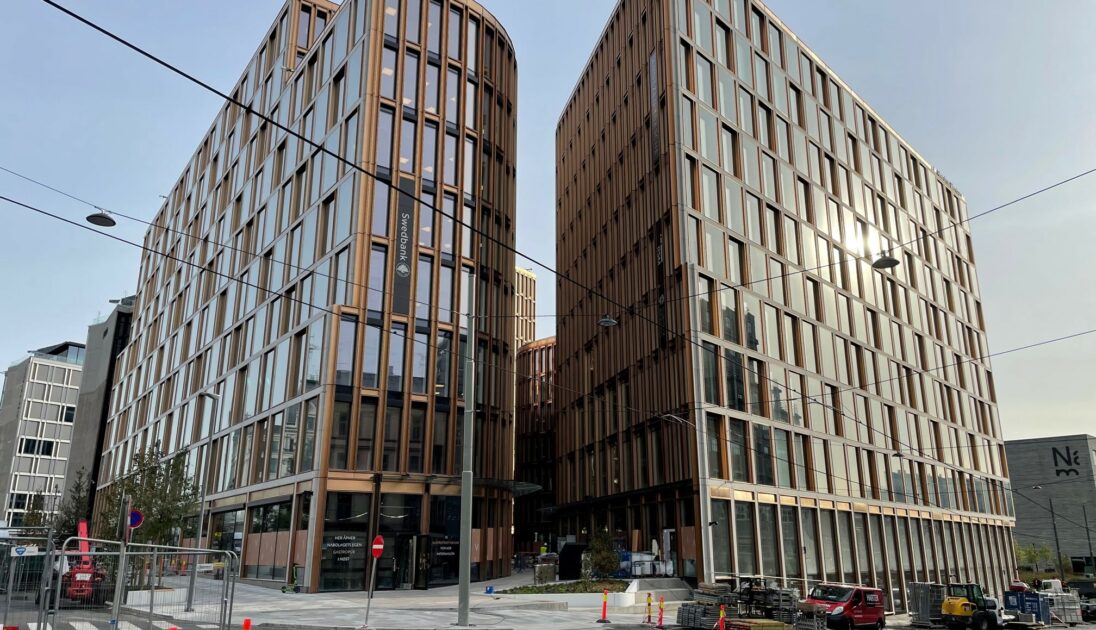
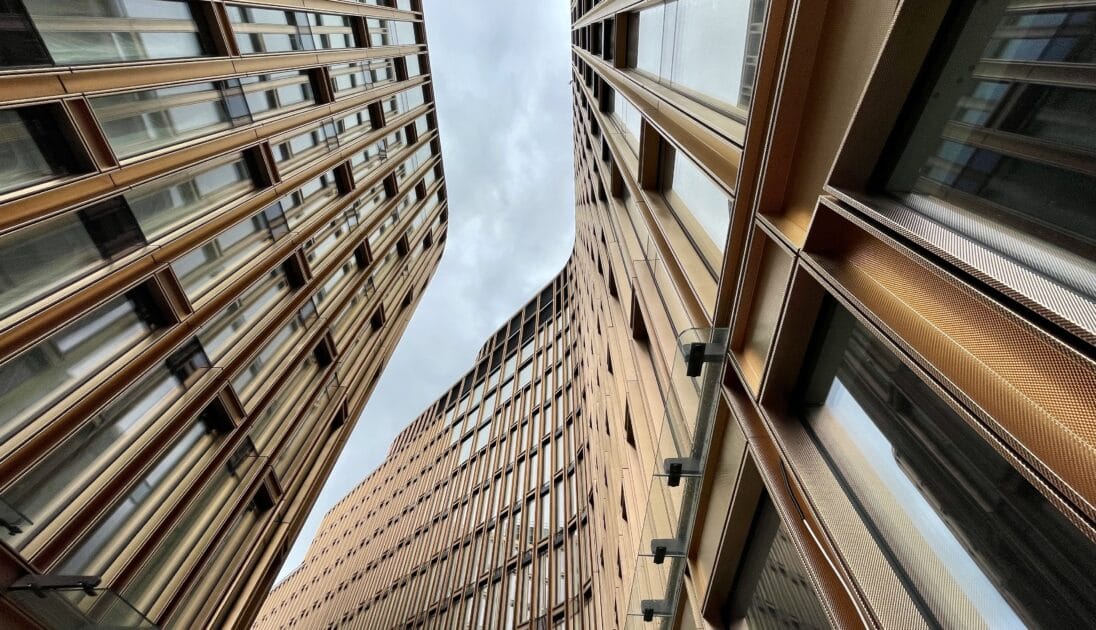
3 major innovations during the concept design phase
The concept design phase of the Via Vika project lasted more than 2 and a half years. And a number of challenges were solved during this period, from the façade types themselves, through to materials and design of the skylight.
Challenge 1: Façade types
By far the most significant task during the concept development phase was to design a system built on two types of façade – single skin and closed cavity.
The decision to include closed cavity façades in the project was a bold one. No building in Northern or Eastern Europe had such façades, and it was not a requirement of the project to include them.
But Staticus’ façade engineers quickly understood that using CCF would bring a number of advantages. It would help them to tackle one of the project’s biggest technical challenges – how to have blinds that could be easily maintained on the external façade. Here is Giedrius Valantinas, Project Manager for the Via Vika project, to explain more.
Using closed cavity façades also brought a range of other performance benefits. The CCF units designed by the Staticus team offer very good thermal insulation (0.54 W/m2K). They also give excellent sound insulation.
As a result of the decision to use CCF, the team had to devise a solution incorporating two façade types.
The final proposal put forward by Staticus, based on closed cavity and single skin façades was selected for the project because it was the best fit for the project’s performance requirements.
Challenge 2: The materials
For the cladding, the original proposal was to use copper for its visual effect. However, previous research and tests by the Staticus team indicated that there are higher levels of pollution from using copper, and this pollution gets into a city’s water management system. That is because when it rains the copper ionizes (this is due to acidity in the rain itself).
So instead, the designers proposed using stainless steel coated with titanium coating. This achieves a similar visual effect to copper, but at a lower cost to the environment. Plus it will keep the same visual appearance for its entire lifetime.
Along with stainless steel, the project also included working with natural limestone, which also meant the cladding needed to be carefully planned at the preproduction stage.
Challenge 3: The skylight
The Via Vika project design included one very adventurous feature – a skylight 12 meters in diameter built into the ground level on the pavement between the two buildings.
The effect for visitors is stunning. Travelling on escalators below the skylight, the effect for visitors is akin to being in the bottom of a canyon. The two Via Vika buildings loom over them as they slowly ascend.
But achieving this effect presented a significant design challenge. In the end, the Staticus design team created a solution utilising 12-metre steel beams and huge horizontal glass panels that are 6 metres in length and 3 metres in width.
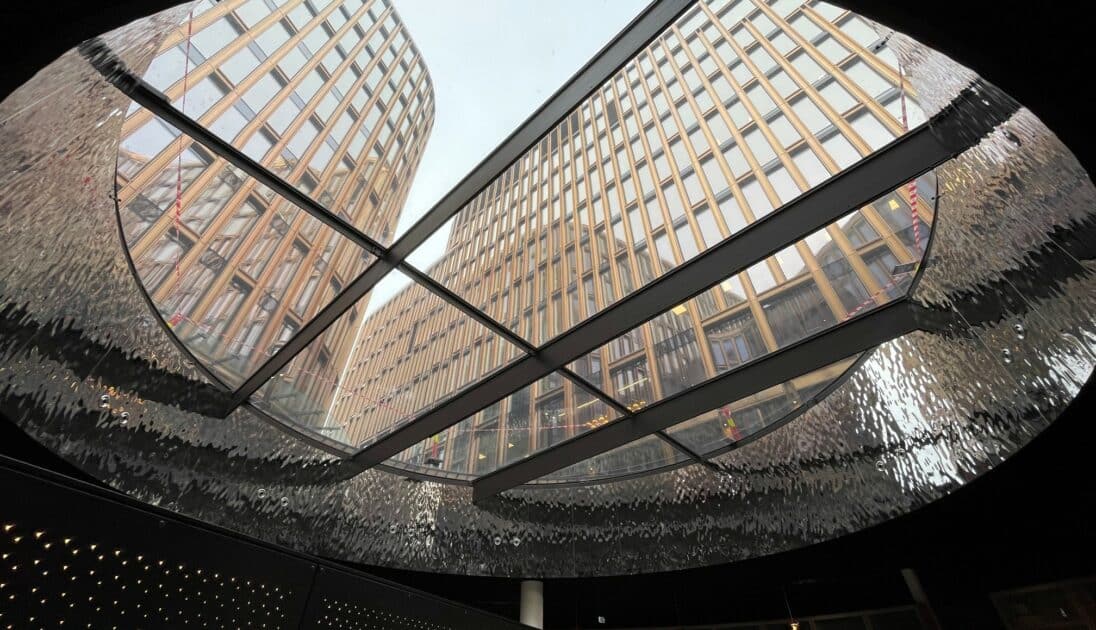
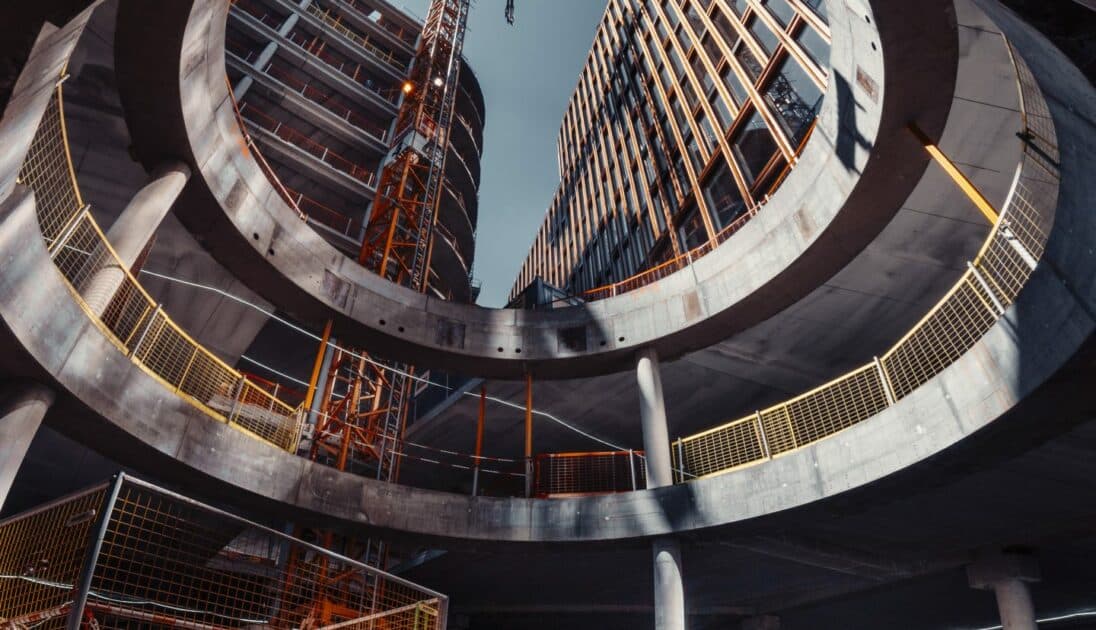
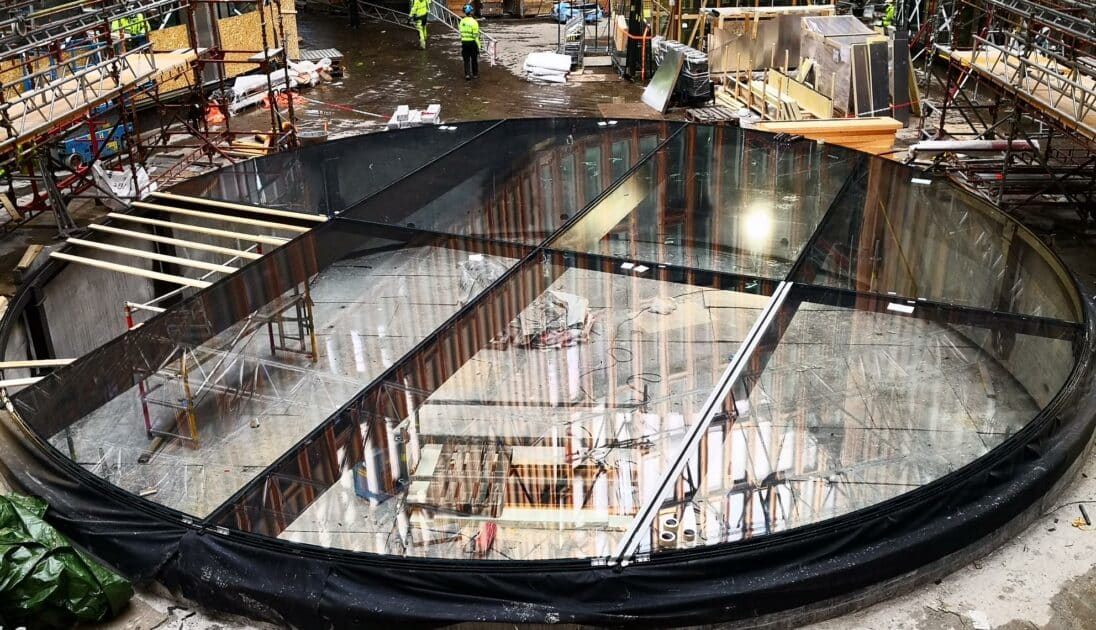
Proceeding to mock-ups and testing
With the design concept approved, the next step was to develop mock-ups and carry out testing on the façade elements.
The Via Vika project team worked together with the RnD, Quality, and Installation departments at Staticus to develop mock-ups of both the closed cavity and single skin façades that would be used in the project.
A series of tests were run in Staticus’ own facility and the mock-ups were approved by the client. They were then un-mounted and shipped to the IFT Rosenheim international test center in Germany. The tests included:
- Water and air permeability testing,
- Wind resistance testing.
Both façade systems withstood water shot as 1,200Pa and 600Pa from a grid of high-pressure nozzles placed in front of them.
With testing complete and the client’s approval already given, it was time for the production of the more than 2,000 elements needed.
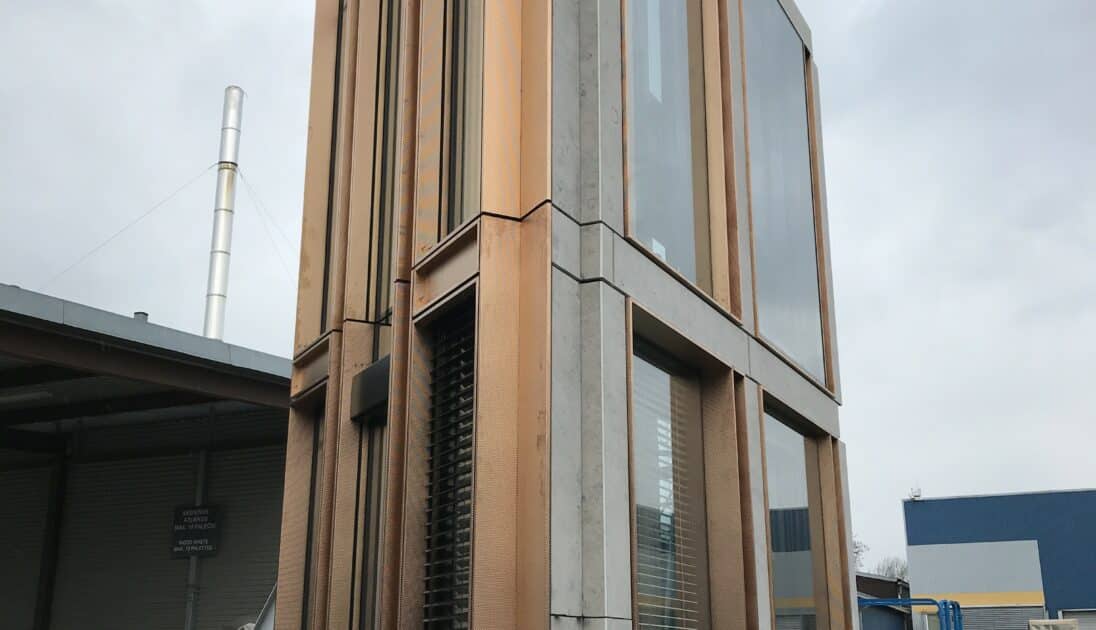
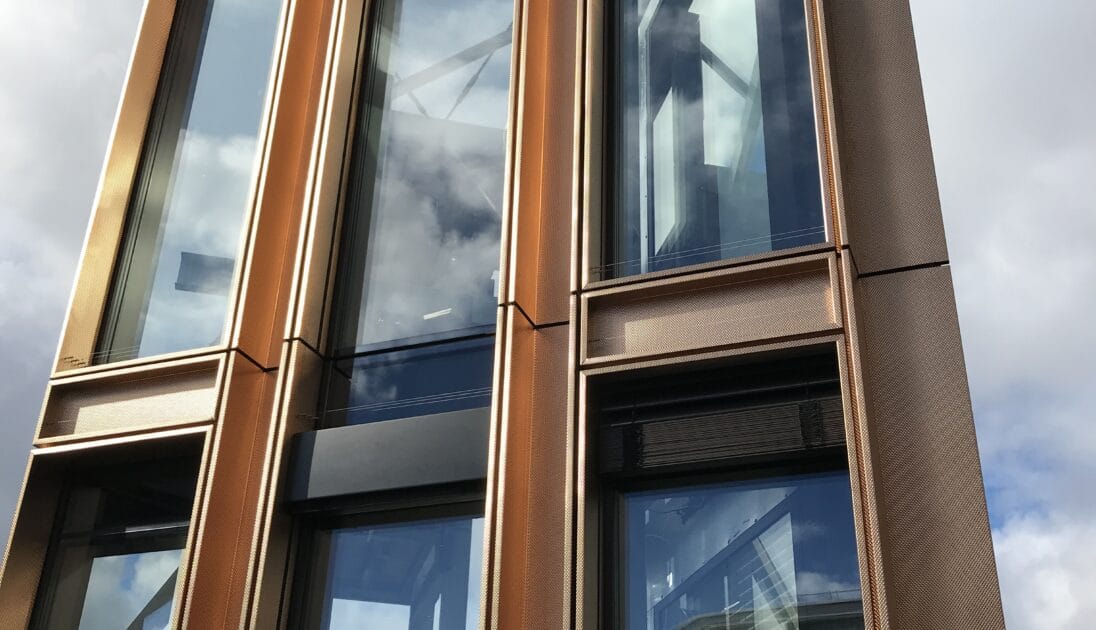
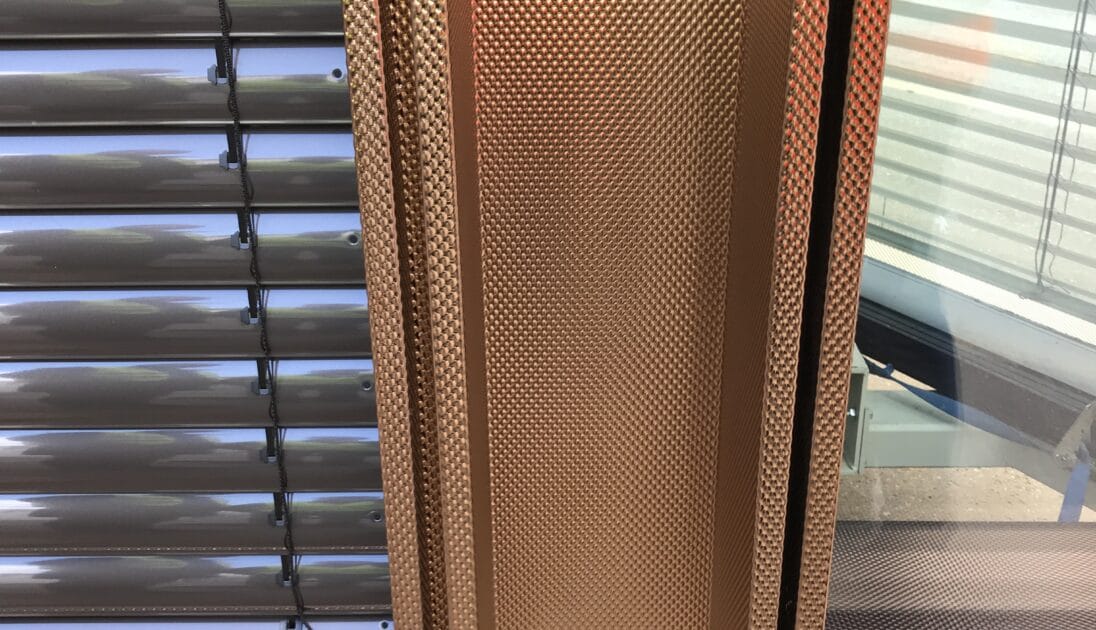