This article is part of our new series on business resilience. Our goal with these articles is to be transparent with our stakeholders on the various ways we ensure our stability and security as we continue to grow and develop. This article focuses on Quality Assurance (QA), and how our constantly evolving XD tool is providing greater transparency for all of our stakeholders. One fundamental aspect of business resilience is managing risks and keeping tight oversight of costs. Effective Quality Assurance (QA) is critical to achieving this.
At Staticus, our aim is to ensure our QA practices are as robust and transparent as possible – our strong track record for delivering high quality on complex, large-scale projects is built on this approach. Our XD reporting tool is a critical innovation in enabling us to continually improve our QA practices while simultaneously helping to foster stronger, trust-based relationships with everyone involved in the project.
Recent additions have taken this tool to a new level of performance, as demonstrated in our latest video on the subject.
Our new video guide shows how stakeholders of the Landspitali Hospital project in Iceland can use our XD reporting tool to track progress and pull up QA data
In this article, we will provide some background on how this tool works, and highlight its key role in ensuring the QA level needed to deliver true business resilience.
Staticus XD reporting tool
We started developing our XD reporting tool 3 years ago, and it has been undergoing constant upgrades since then. Via VCAD in Power BI, the tool connects detailed 3D models of our projects with data from a range of ERP and CDE systems.
As the tool’s name suggests, it goes far beyond simply offering 3D models. Indeed, it has the potential for many more ‘dimensions’ to be added. So far we have integrated a 4th dimension, schedules, and a 5th, payments, with more in the pipeline.
Using the tools “Status” view, stakeholders get an instant overview of a façade project’s progress, with elements shown in different colours to indicate which stage of the value chain – design, production, delivery or installation – it is currently at. Then various filters allow for more detailed exploration:
- Stakeholders can search the model by façade element types or floor levels,
- They can apply the X-ray mode to zoom in on specific areas of the building, or use the single unit view to analyse one element in detail,
- They can also filter for the financial status of a project in relation to the amount of work completed and the amount remaining.
In this way, project stakeholders have a new level of transparency while our team can optimise its workflow based on the latest data, with the tool automatically updating 3 times per day.
QA data integrated into our tool
We have been steadily integrating critical QA documents and data into our XD tool at the design, production, logistics and installation phases.
At the design stage
The technical design report in our XD tool enables project stakeholders to manage all drawings and details.
You can create an overview of all the design submissions for a project – these are shown on the building’s 3D model and can then be filtered based on drawing status. All drawing numbers can be easily located within the model, making searching quick and effortless. And each drawing number has active links to technical drawings, with the latest versions of drawings available to review and download.
It is also possible to filter for C status drawings, which are then shown along with their planned release dates. This facilitates improved planning for design stage completion.
Workshop design sheets are also available via the 3D model. These indicate the status of different elements and enable stakeholders to track shop floor drawing preparation and view any questions the design team has. As with technical design, workshop design is shown on the model based on the current status, and these statuses can be bookmarked. Where the status shows “TBC”, this indicates that workshop design information is currently missing. In this way, stakeholders get transparency on the progress of the design process and team members can address situations promptly.
Using our XD tool, clients, contractors, architects and other partners can constantly monitor the design process and locate specific elements and details. Meanwhile, our design teams can work in a streamlined and transparent manner.
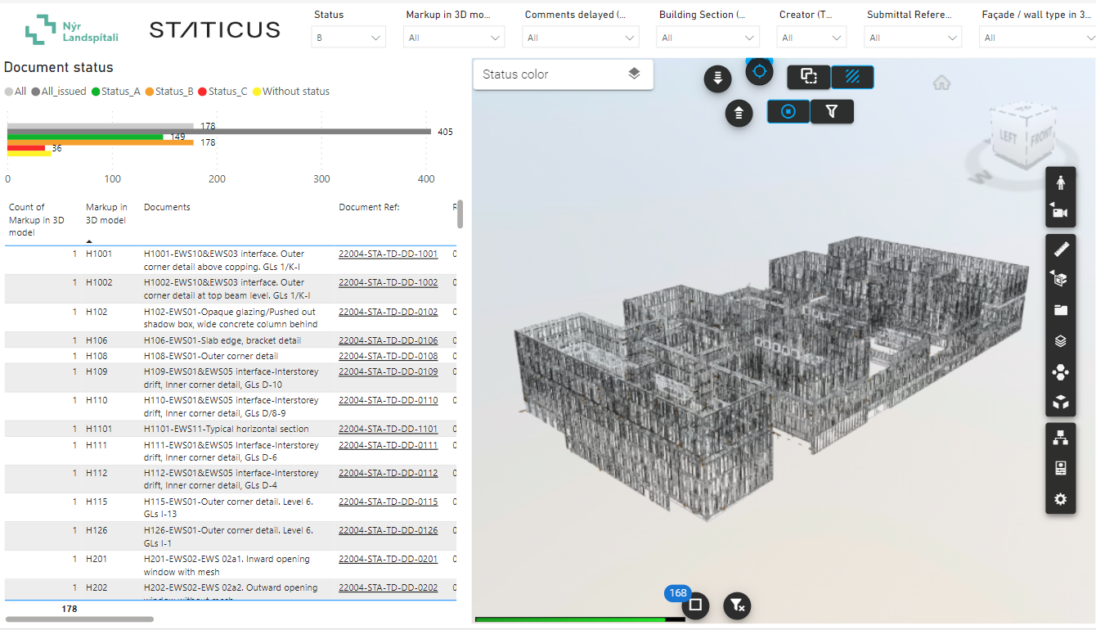
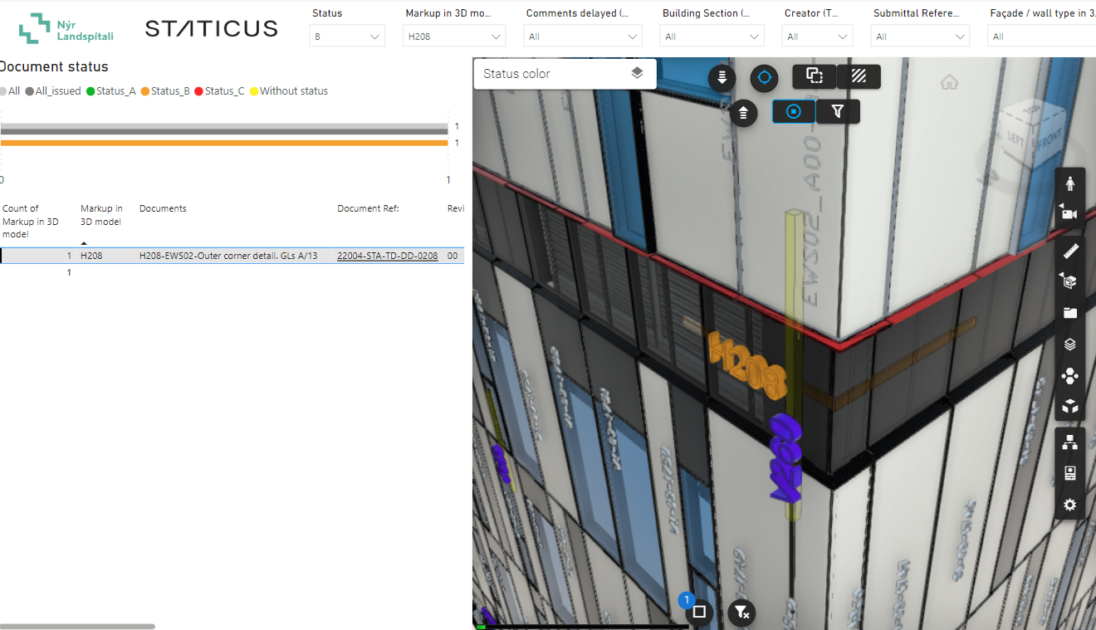
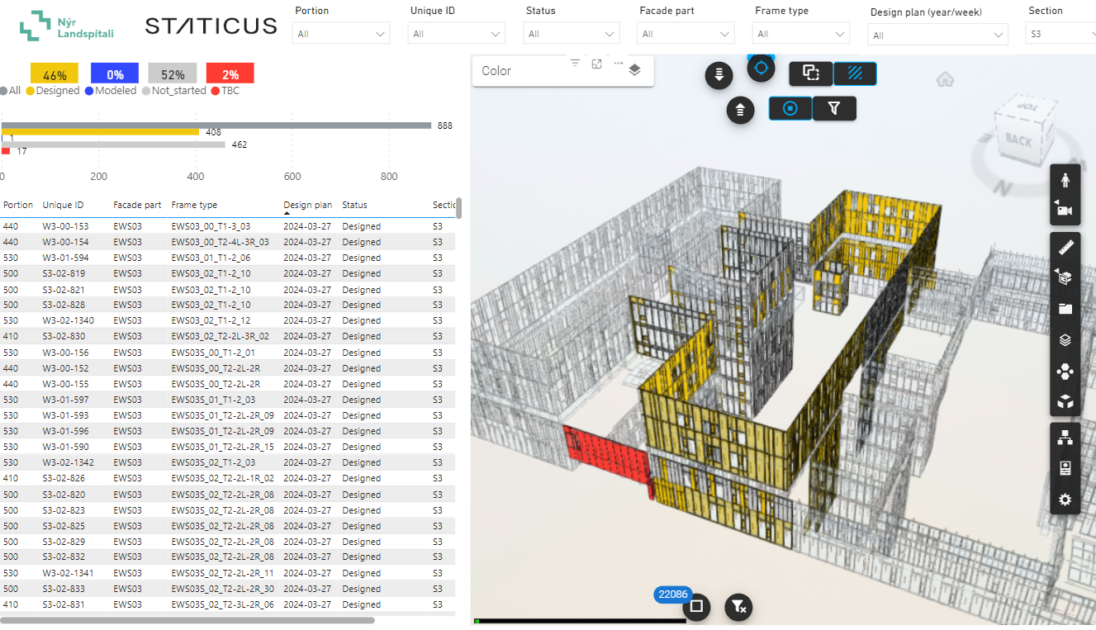
At the production stage
All project stakeholders can easily track production progress simply by applying the filter for incomplete elements. They can then find QA documents attached for each incomplete element, which include details of the materials and technologies that were used for this element. This easy-to-access information accelerates the resolution of nonconformities.
Each element includes an active link to the printed production checklist, which ensures golden thread requirements are adhered to. All production checklists are available to download via a dedicated Sharepoint folder and include visual evidence of unit completion.
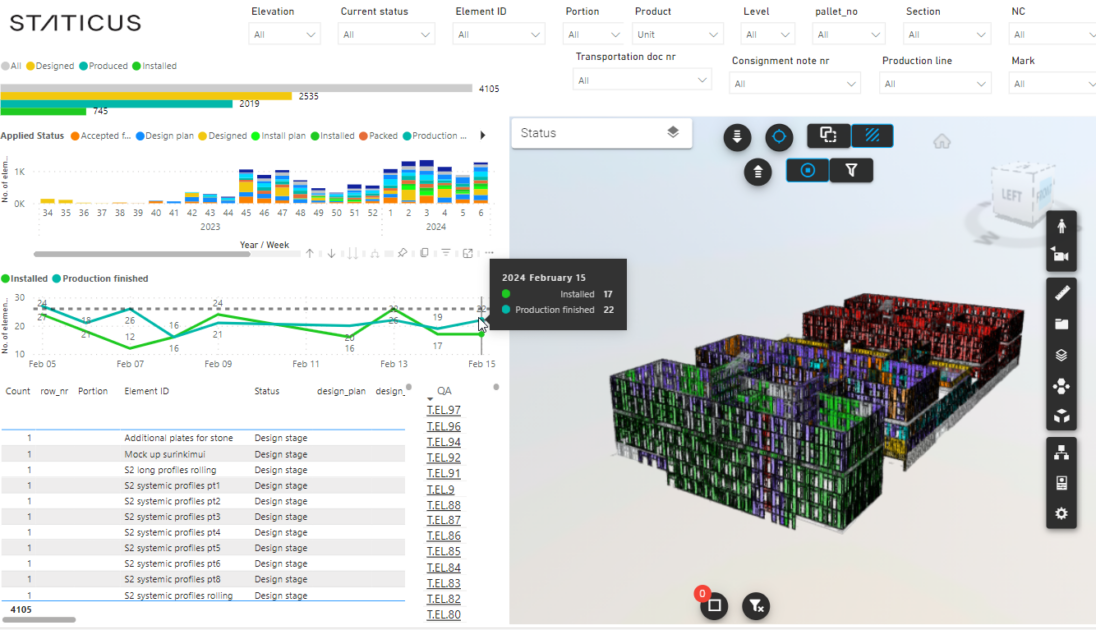
The tool also includes a tracker for production rates over the last two weeks, providing a visual snapshot of a project’s progress. Our production team and project managers can also filter elements based on the production lines being used. This improves assembly-line planning and improves efficiency and QA on complex, large-scale projects.
At the logistics and installation stage
Our XD reporting tool includes details of the shipping status of each element, which facilitates better site planning and management. On the 3D model, stakeholders can apply a filter to see which units are packed into a specific container, improving organisation at the slab edge.
Then once installation has begun, project stakeholders can monitor our team’s daily installation rate. This is shown for the last two weeks and provides a quick and precise indication of how installation is progressing.
Installation checklists can be accessed via links in the XD tool for each individual element that has been installed. These checklists are available to download and include QA checklists and visual confirmation of installation.
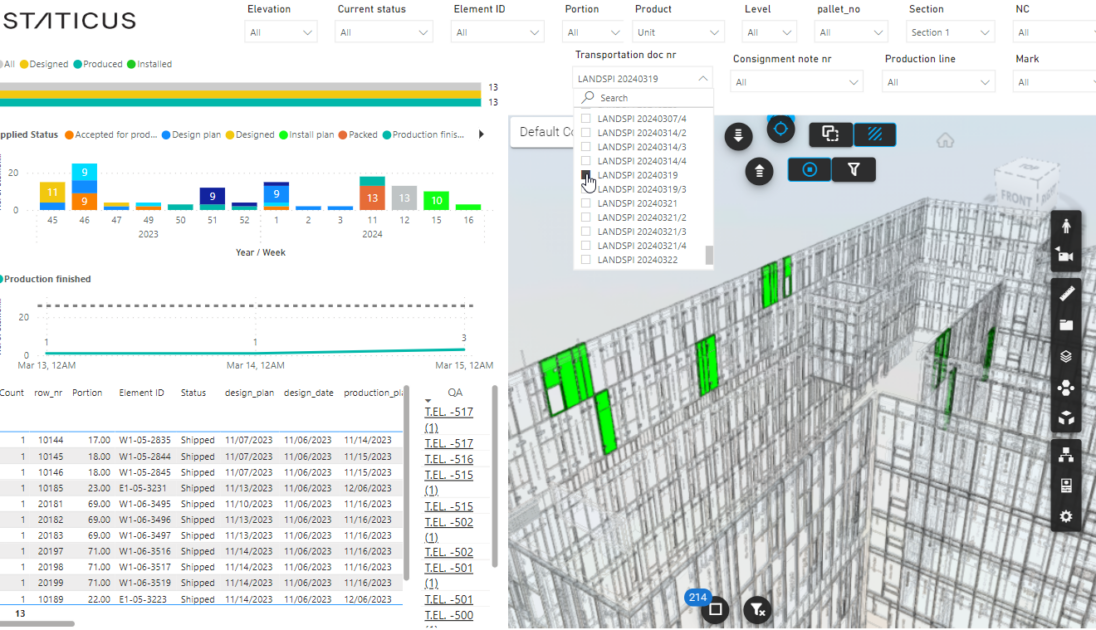
The installation checklists ensure the installation process is completed accurately and efficiently.
Improved QA unlocks new potential
As we increasingly work with top-tier clients, our robust QA practices are critically important. They are central to ensuring our strong track record in the industry is maintained, while strengthening our ability to deliver large-scale, complex projects at very high quality levels. Our XD reporting tool plays an important role in ensuring effective QA on every project. It also provides new levels of transparency and clarity for our stakeholders, improving communication between them.