As a people-first organisation, we prioritise Health & Safety (H&S), and are working continuously to implement best practices in this field. This includes Health & Safety at work reports using UK market standards. The reporting process, which covers 20 different topics related to facade installation, is now being rolled out beyond the UK market to all Staticus projects.
Rasa Sujetienė, our Head of Health & Safety, and UK Health & Safety Manager Bilal Emiroglu told us more about these plans. Rasa also shared details of a recent keynote speech she delivered at the Employee Health & Safety Conference, the largest H&S event in Lithuania.
Adopting H&S best practices from the UK
Following best practices in the UK, the Staticus team has implemented Health and Safety at work reports that track and document onsite Health & Safety practices. “Our historical performance in the UK shows low rates of work-related injuries and ill health, and we are learning from best practices in the country,” Rasa explains.
“Currently, we are using this reporting approach for our UK projects – in this market, they are common. And we are now working on plans to implement these reports in every project we are working on.”
Reports that cover a wide range of H&S topics
So, what exactly goes into our Health & Safety at work reports?
“We evaluate 20 topics in the report,” Rasa explains. “There topics include: Scaffolding, Mobile Elevating Work Platforms (MEWPs), Platforms, Manual Handling, Lifting Operations,
and Work at Height (including leading edge and exclusion zones).”
There are detailed questions for each topic, and as Bilal explains, these questions go beyond simply meeting the necessary regulations. “Of course, they cover every aspect of the safety acts and laws that we need to comply with,” he says. “Beyond these, it is also important to have questions related to the specific activities of facade works.”
“For example, in a typical commercial building project, the facade contractor is the only one using a spider crane. So the report should include questions related to this lifting machine:
- How should it be set up?
- What are the soft spots that the installation team should be aware of?
- What are the manufacturer’s directions and recommendations?
For a truly successful and risk free workplace or installation area, your report needs to focus on all aspects of the work and standard operations such as the ‘standard panel installation process’.
On-site assessments
Armed with detailed questions on each of these 20 topics, the next step for the H&S team is to gather answers from the site team.
“This is done by going around the site with the Site Manager,” and we also collect information about the compliance of the documents. This includes checking that all certificates, records, and other required documents are kept up to date” says Rasa.
“Furthermore, everything is photographed. This ranges from the condition of the premises and how the work is being executed through to photos of the documents themselves.”
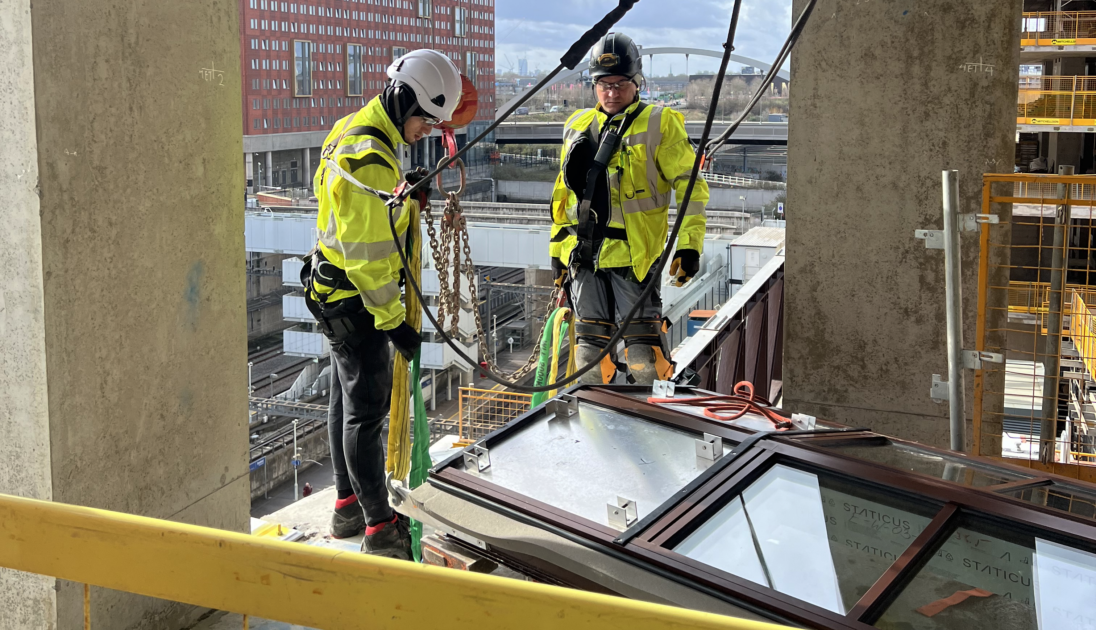
An exemplary H&S record and a more engaged team
Overall, our continuous focus on improving Health & Safety has enabled us to achieve a very strong record. One of our site teams was named in the top 3 for safety scoring on site by a major UK contractor. In 2023, we recorded zero serious accidents, fatal accidents or occupational diseases, and we are targeting zero lost time injuries (LTIs) in 2024.
According to Rasa and Bilal, along with facilitating our pretty good by market standards Health & Safety record, our reports also bring other specific benefits: more measurable H&S assessment; ongoing improvement; and increased clarity.
Measurable H&S assessments
“This approach to reporting means that we have a single unified assessment scale,” Rasa points out.
“Giving sites a safety score based on the items you have checked makes site performance measurable,” continues Bilal. “In this way, you can see patterns and you have the chance to investigate what the root causes of any changes are. And if you apply this consistently, you get a fact-based performance evaluation chart for a specific time frame.”
“Gathering these statistics means we can compare the performance on different projects, or track a project’s progress month by month,” concludes Rasa.
Encouraging ongoing improvement
“These reports provide site managers and teams with an opportunity to compare their projects with others,” says Bilal. “When we clearly explain the mechanics of the reporting and scoring to them, the report score becomes much more than just a number – it is an assessment that encompasses a lot of different on-site activities evaluated from the point of view of safety.”
“This reporting system gives the site team new opportunities to monitor their safety performance and compare it with similar projects, motivating them to continuously improve their own safety measures on site. Additionally, we are having monthly safety meetings internally to share recent activities, news, good practices and lessons learnt.”
It is also a way for site teams to learn about new approaches, says Rasa. “This setup helps us to share best practice between our teams. It creates a new level of transparency that encourages improvement.”
Strong clarity on H&S
The presentation of our reports is designed to be easily understood by every team member. “There is a summary with visuals on the title page, making it easier to grasp the key information quickly,” says Rasa. “The visualisations throughout the report make it user-friendly for our teams.”
“This means we are communicating clearly on the results of our audits in a way that is transparent and understandable for our site teams and stakeholders. The post-inspection scoring is also an important change that has been introduced and has helped any reader to get a quick idea of the health and safety situation on a construction site.”
Sharing insights at the Employee Health & Safety conference in Lithuania
While Staticus’ Health & Safety team are hard at work rolling out this reporting process internally, they are also dedicated to improving H&S practices across the wider industry. That is why Rasa shared Staticus’ experience of implementing site reports at the Employee Health & Safety conference in Vilnius, Lithuania on February 1.
In a keynote entitled “UK occupational safety audits using UK market standards: good practices and insights”, she told the over 1,000 conference attendees about our unique approach to reporting and its positive results.
“I am proud to have had the opportunity to share our best practices with others,” she comments. “I have attended this conference in the past and am glad that other Lithuanian companies are paying attention to Health & Safety and implementing best practices from abroad. As the only construction industry company as a speaker at the event, it was important that our voice was heard. Construction is one of the most dangerous industries, so it is important for companies in our sector to pay close attention to Health & Safety.”
Rolling out our reporting process
The Health & Safety team is now focused on extending the use of Health & Safety at work reports to all our markets and projects. “We plan to use such type unified reports in every project we are working on and to award points after the inspection,” explains Rasa.
The team is also considering ways to roll out this reporting process beyond the installation team. “This is definitely doable with input from other departments,” says Bilal. “When creating the questionnaires, we will need help in understanding the specific processes. For example, if we want to apply a reporting system for production we will face some challenges like getting more familiar with the processes, activities and the machines there. We will need to combine our vision for H&S with specific knowledge provided by experts in the production team. In this way, we will create the most effective reporting system.”
Given the successes Rasa, Bilal and the H&S team have achieved in implementing an effective reporting process for installation, this roll out has every chance of success.