The demanding and complex requirements of the façade for the HUB Victoria renovation required many qualities from the Staticus team. These included:
- Digital innovation in the form of advanced 3D modelling and BIM integrations for enhanced collaboration and coordination.
- Attention to detail managing the complex logistics and site requirements of a renovation scheme located on one of London’s main arterial highways.
- And a commitment to long-term quality manifested in a façade that meets high-performance criteria and sustainability goals while faithfully realising the architectural vision.
The result is a façade that was shortlisted for Renovation Project of the Year (UK) at the 2024 SFE (Society of Façade Engineers) Awards.
We spoke to 3 Staticus team members who were heavily involved in delivering HUB Victoria: Project Manager Aivaras Juodis, Aaron Dehara, our UK Regional Director, and Head of Installation Modestas Midveris. They told us more about the importance of this project and the challenges we overcame to deliver it.
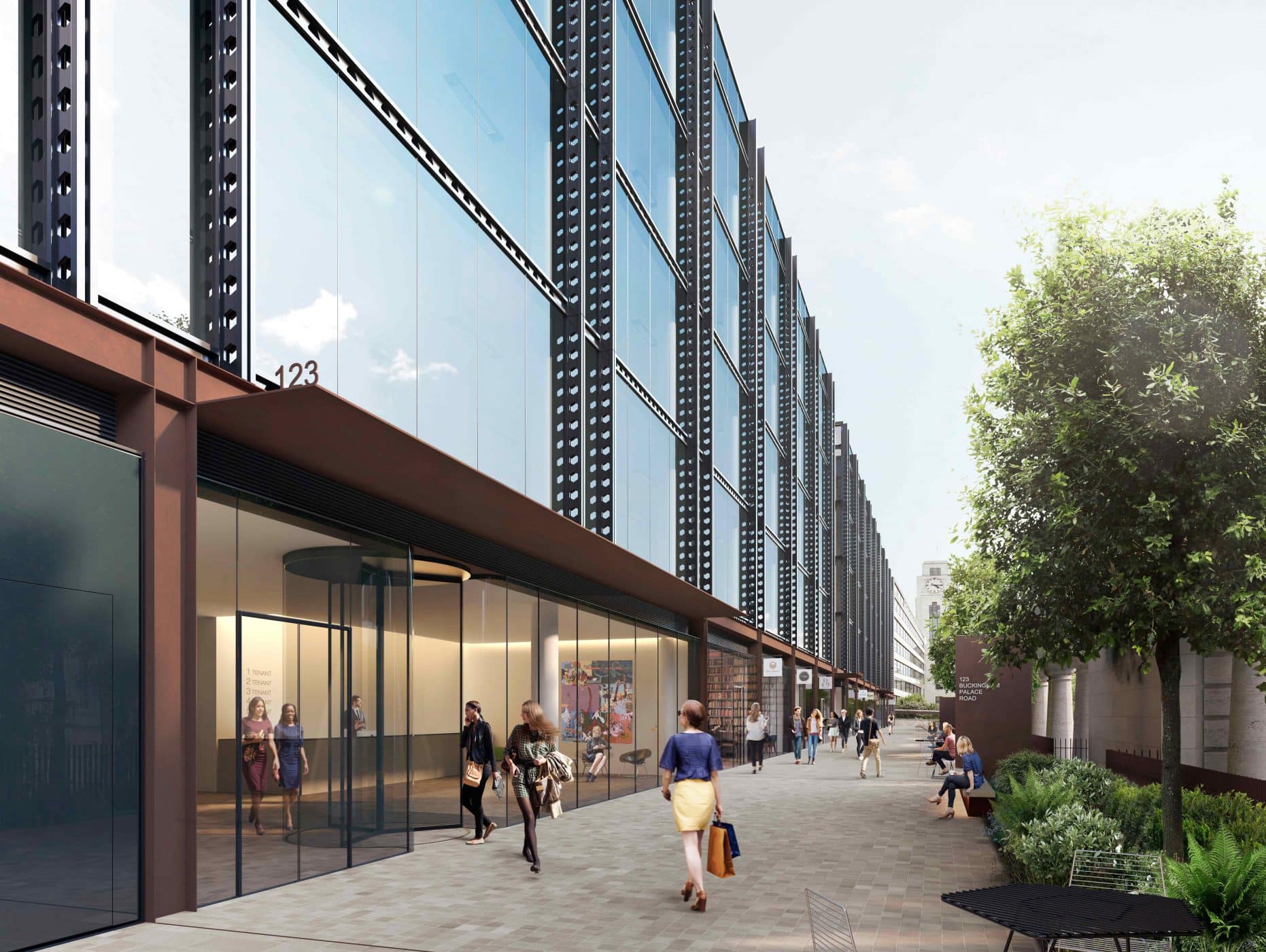
A renovation project with a coherent architectural vision
“There is significant attention being paid to renovation projects in the UK market at present, which makes the HUB Victoria project particularly important and interesting,” says Aaron. “Developers and architects are paying ever greater attention to embodied carbon – the CO2 generated at the production stage of a building. Research indicates that embodied carbon can account for a third of a building’s total carbon footprint.”
“Using low-carbon materials is one way to tackle this problem, and is something our R&I team is working on extensively,” Aaron continues. “Renovation is another. You can reuse existing material in a building rather than producing new raw materials, which is often carbon intensive.”
“The complexities and challenges of renovation projects and material reuse is a topic we have been looking into for some time. The HUB Victoria project has afforded us another valuable opportunity to understand the practical realities when it comes to renovation.”
HUB Victoria is located next to Victoria Coach Station in central London. The renovation of this building involved major improvements to existing ground floor commercial units, office entrances and public spaces, and the construction of a substantial rooftop extension.
It comprised a ‘base’ featuring a stone screen along Buckingham Palace Road, a modern ‘middle’ section with an exposed steel grid, and a ‘top’ section that mirrors the existing building but uses lighter cladding. The end result is a stunning development offering over 30,000 m² of grade A office space.
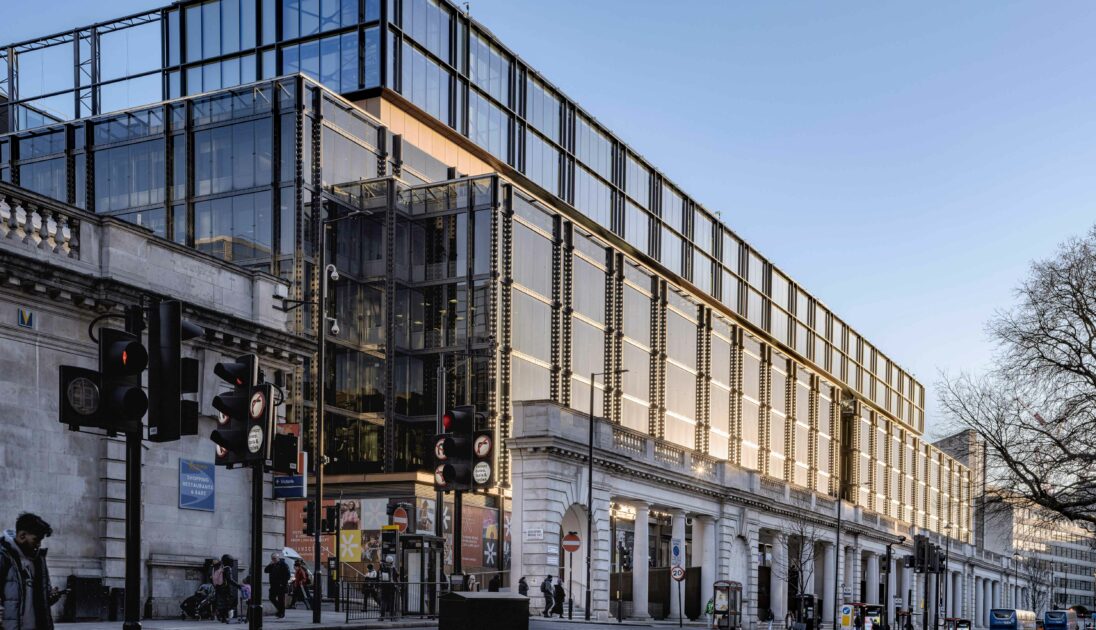
“Along with their sustainability benefits, renovation projects make valuable architectural contributions to our cityscapes,” comments Aaron. “This is certainly the case with HUB Victoria, where the new extension blends tastefully with the existing building.”
A multi-faceted façade
“The scope for the HUB Victoria façade was wide-ranging and complex,” explains Aivaras Juodis, who was Staticus Project Manager for this project.
The renovation created two building types. From level 6 to 7 there is a new extension. Then the below-ground entry levels are refurbished. So the façade included new concepts for the new part of the building, along with the appropriate replacement and extension of the existing exterior.
“This meant we had to apply two different approaches to this façade – a unified design for the new structures and adaptive methods for retrofitting the existing ones,” explains Aivaras. “Overall, the project’s technical design development lasted approximately 8 months. The end result was finalised designs for 10 different façade cladding types and external structures.”
These 10 types broke down into 5 main categories:
- Unitised façade. We created fully glazed units with pre-installed vertical and horizontal fins installed onsite.
- Stick façade. The project features 4 types of stick façade, including simple underslab standing stickwork and 3-story high stickwork connected to the main structure with only 3 bracket lines. Some of these incorporated fully automated AOVs.
- Composite panel walls. Installed around the building’s perimeter, these feature an aluminium cladding system and aluminium soffits.
- Lift shafts. We installed 2 self-standing 9-storey lift shafts, which were half-lambert glazed and half-aluminium clad.
- Double-skin façade glazing replacement. This was used to replace 2 floors of old double-skin façade glazing. Doing this was particularly challenging due to the outdated solutions being replaced and the need to redesign parts so that they met the latest regulations.
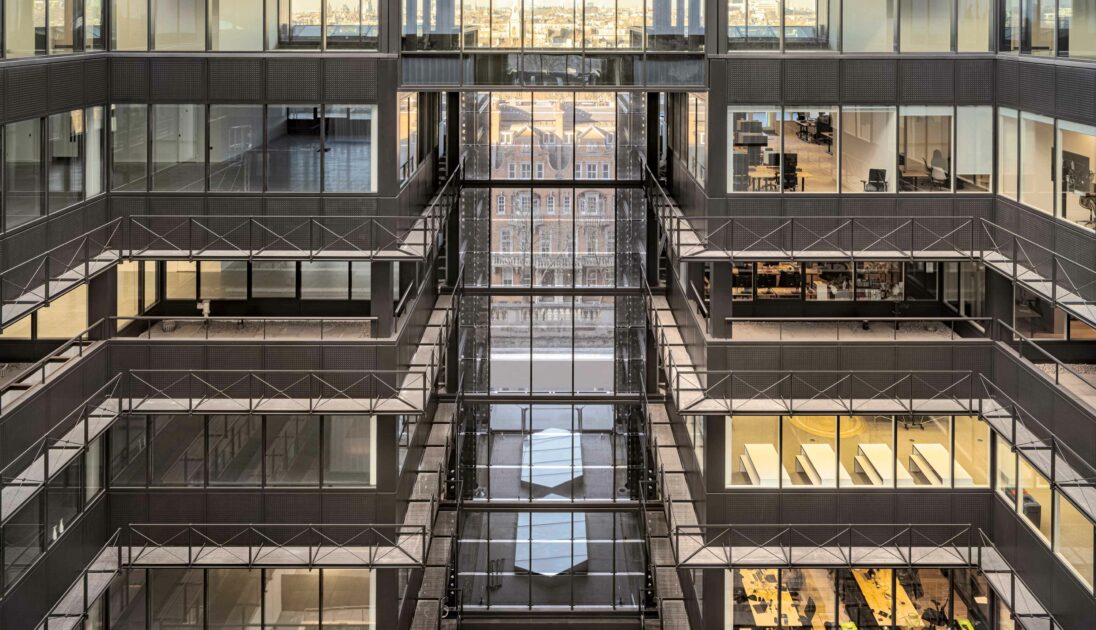
“It took a lot of expertise and adaptability from the team to design and deliver such complex solutions,” says Aivaras.
The HUB Victoria façade in numbers
- Façade package in total: 11,472 m2
- Unitized façade: 3,835 m2 (654 panels)
- Stickwork Curtain Wall: 3,117 m2
- Cladding: 2,882 m2
- Other types (rainscreen, balustrades, soffits AOVs): 1,614 m2
Various challenges to overcome in a tight timeframe
“Our team started working on concept design in early 2020 during the tender stage,” says Aivaras. “It took 8 months to develop designs for the various elements. Then production kicked off in October 2021. Installation began one month later, and was completed in August 2023.”
“Delivering such a complex project over this timeframe required us to keep resilient and focused,” Aivaras continues. “Some of these complexities stemmed from the fact we were working on a renovation. For example, with renovation projects, coordination between the different partners involved is both more important and more challenging. We needed to find a way to enable effective data sharing and communication.”
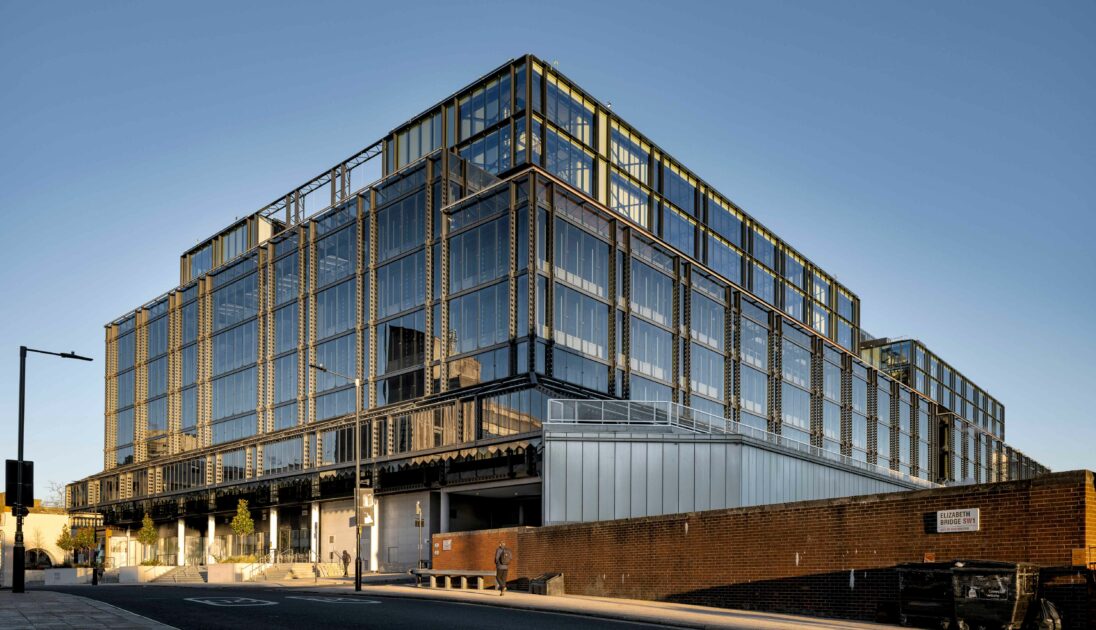
“Other challenges related to the architectural and sustainability goals,” explains Aivaras. “The project was targeting BREEAM Excellent certification for the rooftop extension, and emissions that are 61% lower than the London Plan’s baseline. This put high-performance demands on the unitised façade. Then there were the overall quality standards expected for this project.”
“Finally, the site itself raised a number of technical challenges. Essentially, we were constructing a new building on top of an old building situated in the centre of a busy city,” says Aivaras. “Ensuring maximum efficiency on-site and working around logistical problems was essential.”
The Staticus team demonstrated adaptability and expertise in overcoming these challenges.
Challenge 1: Effective coordination on a renovation project
With any project, effective coordination between teams and partners is important. In the case of renovations, it is even more critical, as Aivaras explains. “Working with existing structures brings added complications,” he says. “The as-built information is not as accurate. What’s more, the lack of modelling means clash detection isn’t possible, so there is a risk of differential movement between the joints of the new build and old build.”
“In the case of HUB Victoria, as-built information was frequently missing, or was not at the required accuracy level,” Aivaras continues. “The drawings of the old façade lacked clarity, particularly for the interfaces between the new and old façades. And missing markups made it difficult to locate the relevant drawings.”
To ensure effective coordination for the project, and enable clash detection, the team needed a centralised and shared repository of accurate information for both as-built and new structures. “Unfortunately, the buildings had not been 3D scanned and then modelled into the BIM,” comments Aivaras.
“After each survey of existing interface structures, data was continuously integrated within a shared BIM model, including our façade design,” explains Aivaras. “This enabled real-time coordination internally, and with structural and mechanical teams, which facilitated early clash detection and resolution. This was essential on a project like HUB Victoria, where complex solutions were often required. For example, the differential movement between the new and old buildings required large expansion joints.”
Regular BIM meetings and shared digital models further enhanced communication and improved decision-making on the project, cutting out errors and the need for reworking.
“This integrated approach allowed us to achieve a seamless and efficient reconstruction process with all stakeholders,” comments Aivaras.
“In the end, by precisely measuring the existing structure and integrating this information in the BIM, we were able to ensure the façade components aligned perfectly with all structural supports and mechanical systems,” concludes Aivaras.
Solution 1: Avoiding demolition while upgrading glazing
“The original plan for levels 1 and 2 was to demolish the existing double-skin façade completely, and construct a new one, which would include maintenance gangways,” explains Aivaras. “However, we believed an alternative route was possible. After surveying the existing structure, we found that it was in good condition. So we developed a new solution that would leave almost the entire existing façade-bearing structure in place. Now, it was only necessary to replace the glass.”
“This solution was approved, and we procured new glass and glass-holding profiles that matched the existing ones,” continues Aivaras. “The result was reduced waste and the avoidance of unnecessary demolition. We were able to extend the life cycle of the existing structures, which saved on embodied carbon. This option also led to cost savings for the client.”
Challenge 2: Meeting ambitious sustainability goals
By choosing to make HUB Victoria a renovation project, client GAW Capital had already locked in significant savings in terms of embodied carbon. They set further ambitious sustainability targets for the project, and the façade was critical to delivering on these.
“With contemporary façades, clients are looking for low embodied carbon and low operational carbon,” explains Aaron. “Achieving both of these while delivering the necessary quality standard is never straightforward, and requires adaptability and expertise. Our design team found a range of smart solutions for HUB Victoria that enabled significant savings in embodied and operational carbon, resulting in the the project being awarded BREEAM Excellent certification.”
Solution 2: High-performance glass cuts operational carbon and boosts well-being
“The unitised systems we developed incorporated high-performance glazing,” explains Aivaras. “By enhancing the building’s energy efficiency, this solution has contributed to a significant reduction in operational carbon emissions. Naturally, this solution also delivers reductions in heating and cooling costs. Furthermore, by improving the natural lighting and creating a comfortable temperature, this solution makes the interior healthier and more comfortable.”
Challenge 3: Delivering on quality standards and efficiencies
“Our team was thorough and dedicated to finding the right design solutions to solve technical challenges and deliver efficiencies where possible,” comments Aivaras. “We followed an iterative process that involved extensive surveying. We applied the findings from these surveys to ensure the seamless integration of the new claddings and structures with the extended and refurbished buildings.”
“We employed a unified design approach for the new structures, and used adaptive methods for retrofitting the existing ones,” Aivaras continues. “We also identified areas where cost savings were possible without any loss in quality or performance. For example, we omitted the glass privacy frit on level 6 of the building. We also replaced the border frit with border edges using polysulphide mastic and omitted the external feature frame fins overlooking the retained glass atriums in two of the courtyards. These measures all reduced costs for the project.”
Solution 3: Off-site prefabrication
“Also, prefabrication of the unitised façade system off-site was a practical solution in terms of installation and logistics,” says Aivaras. “It also contributed to minimising embodied carbon. With better quality control, we are able to reduce wastage and ensure zero on-site waste generation. Furthermore, prefabricated systems require less machinery to install, enabling another energy saving.”
Challenge 4: A tight central London site with the building still in partial use
During the HUB Victoria renovation project, part of the building remained in use by tenants. Furthermore, its location adjacent to and partially above the busy Victoria Coach Station in London added complexity, as Head of Installation Modestas Midveris explains. “This was a challenging installation. We were effectively constructing a new build on top of an existing building above a very busy transport hub. The site needed to accommodate heavy foot traffic and minimise disruptions to commuters.”
With these logistical challenges, careful planning and the highest health and safety standards were required for the on-site installation.
“A lot of the key work for an effective installation happened at the design stage,” Modestas points out. “For example, taking precise site measurements was crucial to addressing the connections between the old and new façades. We ultimately achieved shadow gaps as close as possible to 10mm.”
Solution 4: Overcoming urban challenges by advanced logistics and on-site efficiency
“Logistics was another factor,” Modestas continues. “We carefully coordinated the deliveries to the site, which were far from easy due to the limited storage options that come with a central London location. Deliveries to the site were often long and complicated – sometimes multiple transfers at intermediate sites were needed. Through careful planning, we ensured minimal disruption along with high safety standards.”
“For the Level 6 and Level 7 extensions, the unitised façade system was installed on-site as a series of factory-assembled units,” explains Modestas. “This brought numerous advantages. The fact that the frames and all-weather seals were applied in a controlled environment significantly reduced installation. There were also reduced site-sealing requirements, so less material was needed on site. ”
“On-site safety was increased thanks to the fact the panels can be installed from the inside, with no external access requirements. And overall, using pre-build frames that are pre-glazed speeds up the installation rate.”
Passing strict CWCT testing
“In the UK, any new façades at the scale of the one we developed for HUB Victoria must undergo CWCT testing,” comments Aaron. “For those outside the UK market, it is worth noting that this testing is very strict in comparison to typical requirements in Europe. Façades installed in Europe usually only need to meet roughly half of what is required by this test, which covers air infiltration, water penetration, wind loads, and impact.”
“A representative of the VINCI Technology Centre testing laboratory – where we performed the test – stated that typically only around 5% of projects pass the CWCT test on the first time and without errors,” says Aivaras.
“Although we did identify one issue with water permeability, the team was able to work on the testing site and they quickly found a solution. After correcting this issue, we passed this strict test, managing the whole process within a week.”
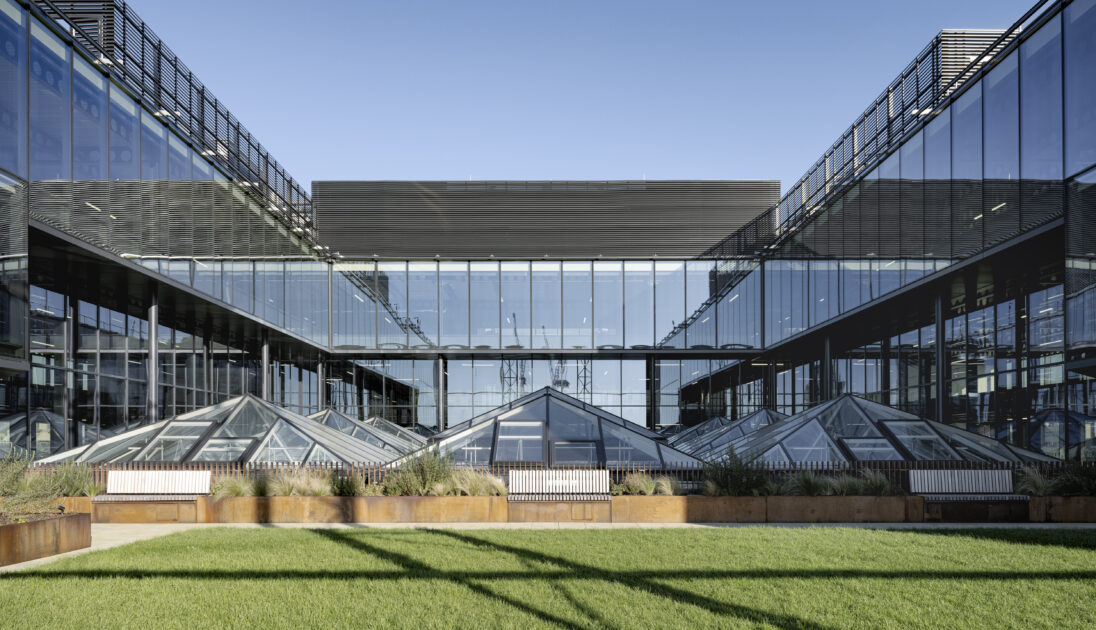
Meeting the highest health and safety requirements
“I am extremely proud of the health and safety standards the installation team maintained on the HUB Victoria site,” says Modestas. “Over the course of the installation, we received McLarens’ Safety Award 3 times. The general contractor, McLaren, has a monthly award it gives to on-site teams working on their projects. The award is based on points awarded in 15 different categories. So, this demonstrates how much care and attention the team was putting in.”
“The team received another seal of approval in terms of fire safety,” continues Modestas. “While delivering this project, Staticus UK was applying for FIRAS certification. The HUB Victoria team was selected for the on-site audit. This meant all of our on-site documentation was checked, and the team had to show the auditors how they work on-site with fire protection products and take a knowledge assessment. Every member of our team passed. What is more, 2 of them are approved as supervisors and 4 more as technicians.