Staticus’ next generation Hybrid Unitised Façade (HUF) system, with a further refined design, is being used on a project for the very first time. Having successfully passed through testing at the VINCI Technology Centre (UK), 190 units of our 2nd generation HUF will now be produced and installed for the Textiltorget project in Stockholm, Sweden. This next level HUF, which has been developed in-house in partnership with SINTEF, OsloMet and KTU, offers significant benefits over aluminium-based façades. These advantages include lower embodied carbon, improved thermal performance, and easier recycling at the end of life stage.
A milestone in our use of timber
Staticus has extensive experience of incorporating timber into façades. Our first project using a custom-made unitised façade that featured timber was in 2012. Since then, across Scandinavia, we have regularly designed, constructed and installed façades that use wood.
Initially, the primary reason to incorporate wood into unitised façades was the material’s excellent thermal performance, which aligns with or even exceeds passive house standards. Over time, another benefit of the use of timber has gained prominence, namely the reduction of embodied carbon. In 2021, we embarked on a research and development project aimed at reducing a façade’s carbon footprint by from 45% to 75%. This is achieved by replacing materials with high embodied carbon with low-carbon alternatives like timber. This led us to design and prototype a next generation HUF system, in partnership with SINTEF, KTU and OsloMet. The research has focused on innovative ways to utilise wood as an alternative to aluminium, along with the incorporation of sensors that connect to the building’s digital twin and the development of AI applications for predictive maintenance.
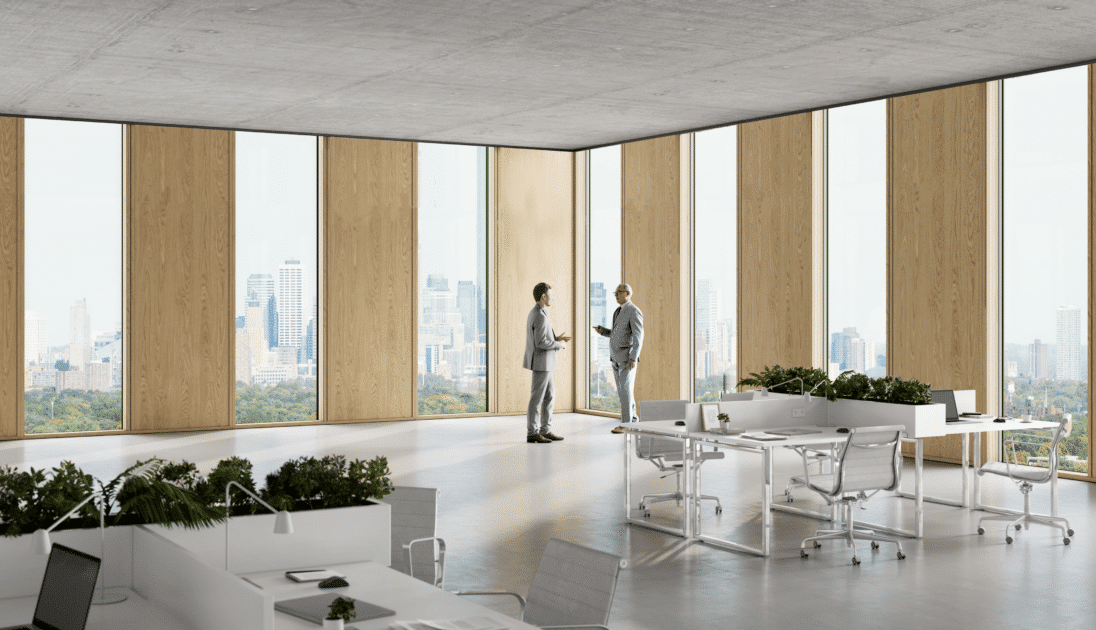
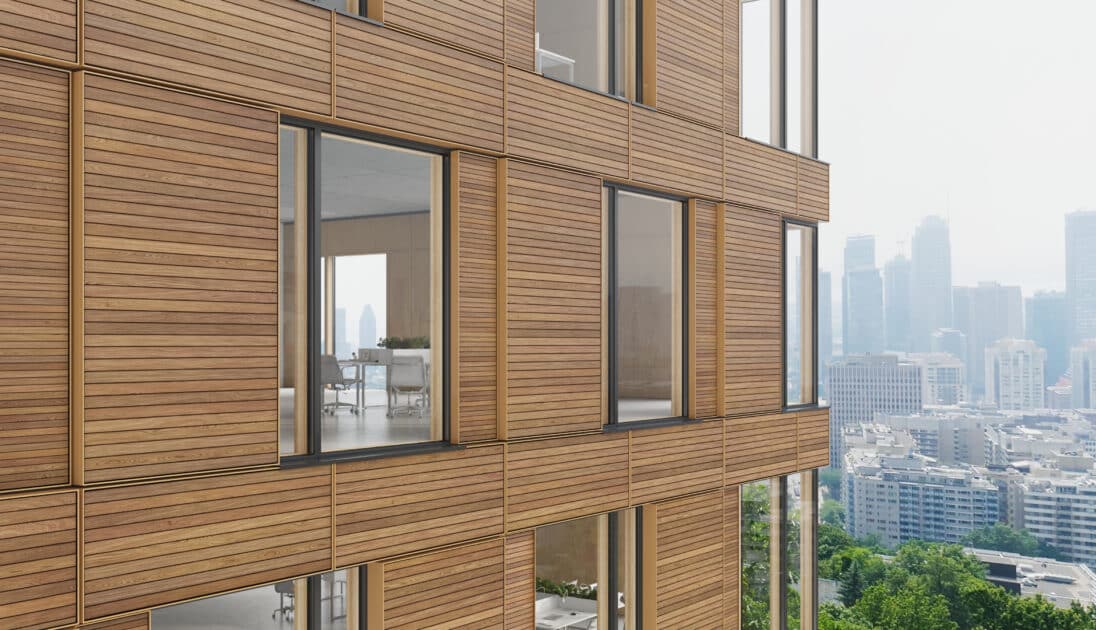
The Textiltorget project represents a major milestone for Staticus as we deploy our newly-developed, next generation HUF for the very first time. In this short article, we will provide more detail on the benefits of HUFs and the process of developing our latest version, and explain how it will be deployed in the Textiltorget project.
Staticus’ new HUF plays important role in carbon reduction
When it comes to its use as a material in façade construction, aluminium has two significant disadvantages. Firstly, it has very high embodied carbon because the process of manufacturing aluminium is energy intensive. And secondly, in terms of thermal performance it does not have a lot to offer.
As a result, Staticus has been further developing its hybrid solutions by exploring the use of alternative materials, which has led to the development of its next generation HUF. Through our Staticus Care division, we secured funding from Norway Grants in 2021 for a project titled “Developing a more environmentally friendly automated façade system that is integrated into the building’s control systems” (project code no. LT07-1-EIM-K01-003). Together with our project partners SINTEF, OsloMet and KTU, we have then worked to develop a next level HUF based on specific client needs related to performance and sustainability.
In this newly-developed HUF, aluminium structural mullions and transoms are replaced with glulam – glued laminated timber. This is a structurally engineered product made up of layers of wood that is glued together using moisture-resistant adhesives.
Staticus’ next generation HUF system brings numerous advantages compared to standard aluminium unitized façades, as our Project Manager Algirdas Simuntis recently explained. At the production stage, it can cut embodied carbon emissions by from 45% up to 75%. During the building’s use, it provides excellent thermal insulation thanks to the cellular structure of wood. Glulam has been shown to be 1,700 times better than aluminium in terms of insulation, and even outperforms brick. And at the end of life phase, glulam is easy to recycle.
Advantages in design and production
Naturally, there are aesthetic benefits to using timber, and Staticus’ latest HUF also has technical advantages in terms of design. With wood frames, it is possible to realise more ambitious architectural visions because there is a wider range of possibilities for playing with frame connection joints.
Site-built wood systems for façades create logistical headaches for other project partners using the site, and increase costs. In contrast, Staticus’ HUFs are fully prefabricated at sizes ranging up to 10m2, and then delivered to the construction site for immediate installation.
The Textiltorget project in Stockholm
After 2 years of development and testing, our next generation HUF system is being deployed in a project for the first time, the striking and technically challenging Textiltorget renovation project in the quayside Hammarby Sjöstad district of Stockholm. This 9-storey building was originally constructed in 1955, and has transformed over the years from a factory into an office building.
Now, in order to improve the building’s energy efficiency and visual appeal, a new façade is being added. We have been contracted by Fabege AB to design, build and install 1,400 m2 of bespoke timber-aluminium hybrid unitised façade based on plans by LINK Arkitektur.
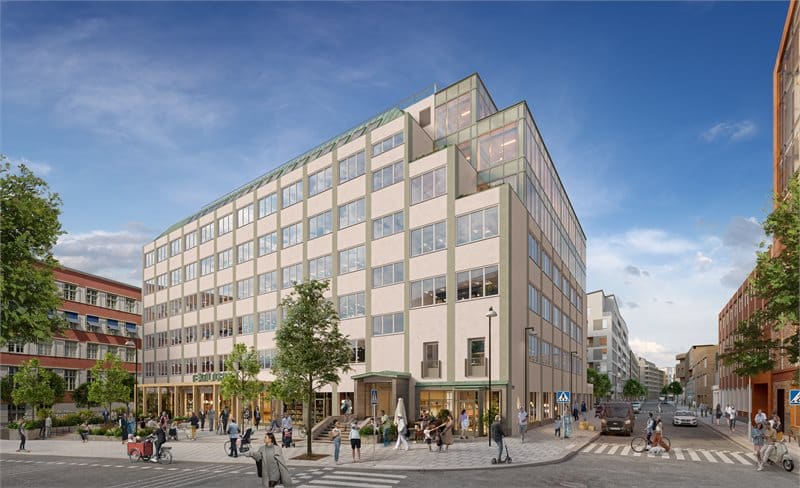
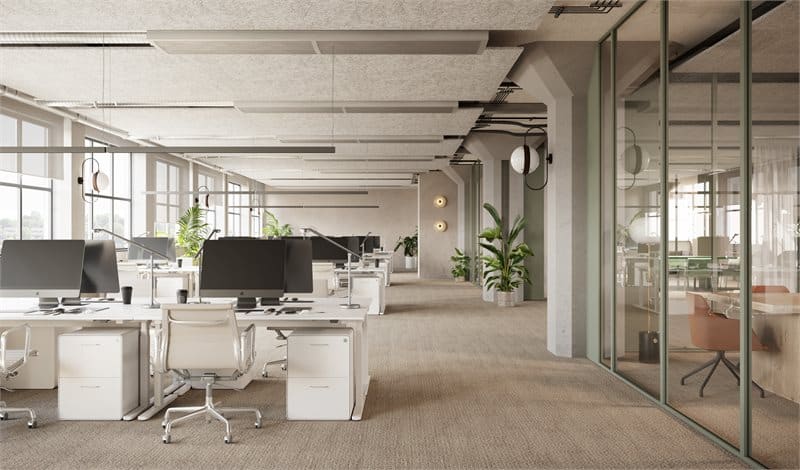
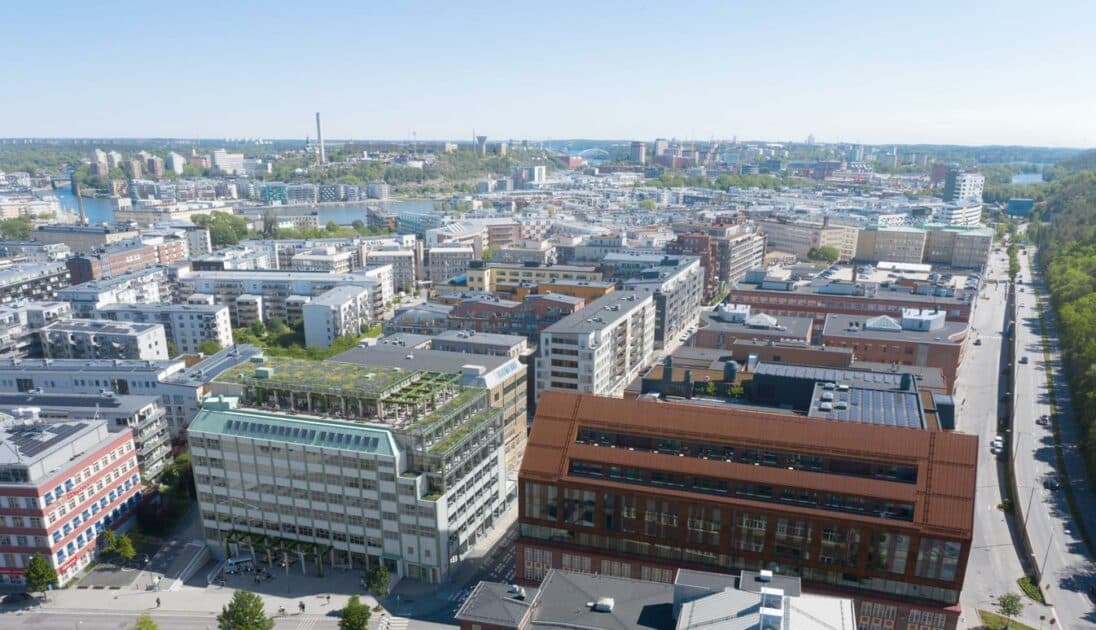
Fabege is targeting very high levels of performance and sustainability for this project. Textiltorget will have BREEAM-SE Bespoke certification at the second highest level, Excellent. This certification imposes high demands on sustainability performance, and one of the project’s objectives is a reduced CO2 footprint. Our next level HUF system will play an important role in achieving these ambitious targets.
With installation scheduled to begin at the end of August 2023, the turnaround for this project is tight. The fact that the façade will be added on top of the existing building also brings additional technical challenges.
Nevertheless, the project is progressing smoothly. One major milestone that has already been completed is the testing to the HUF system to be used in the project. In May 2023, the system passed all necessary tests at VINCI Technology Centre in the UK. The test sequence was as follows:
- Air permeability,
- Watertightness – static,
- Wind resistance – serviceability
- Air permeability,
- Watertightness – static,
- Watertightness – dynamic,
- Wind resistance – safety,
- Impact resistance – safety.
For air permeability, our HUF system received AE classification and a declared value of 900 pascals. For water tightness, it received RE classification and a declared value of 1200 pascals. It was given a +2000 pascals value for serviceability and a +3000 pascals value for safety when tested for wind resistance. And in impact resistance, it was classified as Class I4/E4.

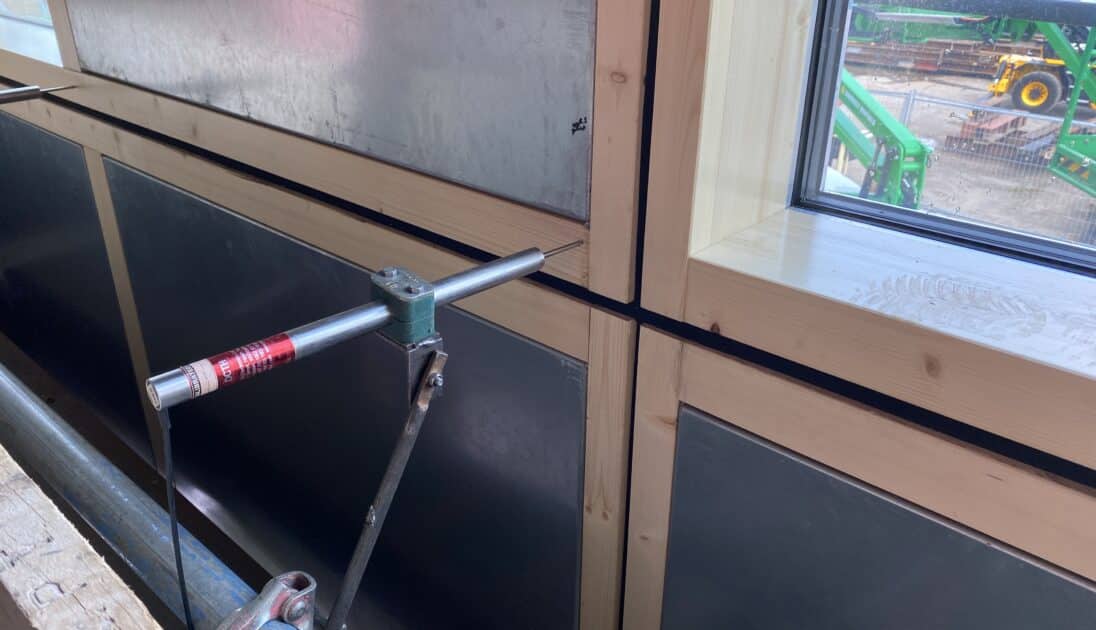
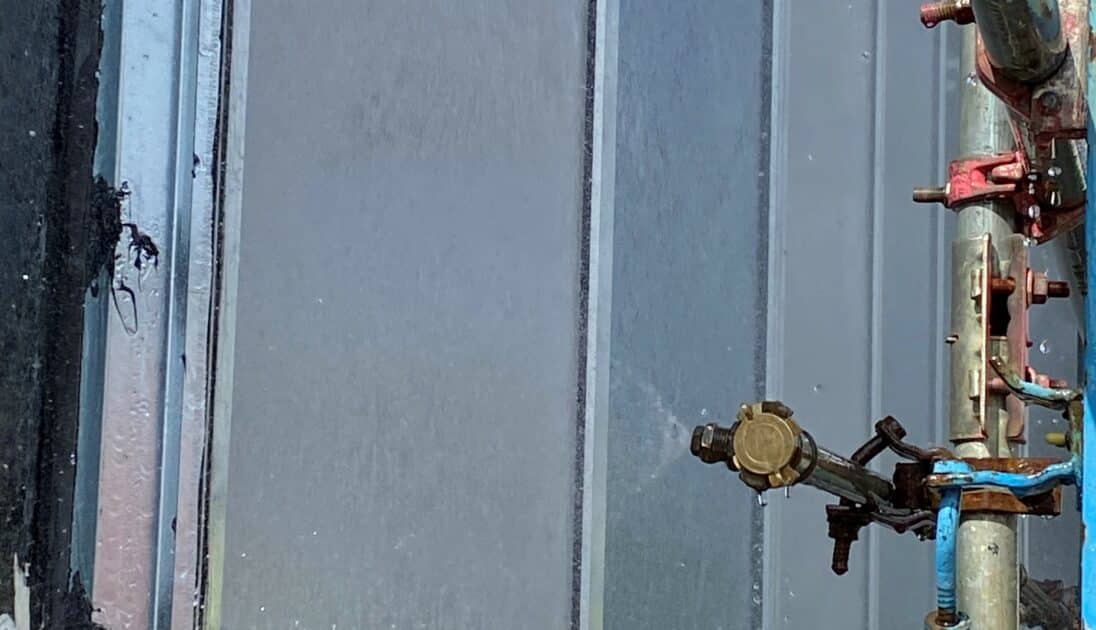
These results demonstrate our HUF system’s suitability for this project and many others. They are the results of our extensive experience working with timber, and the culmination of years of work and dedication by our R&D team.
Just the beginning for Staticus’ new HUF systems
Installation for the Textiltorget project is due to be completed at the end of 2023. The successful completion of this project will represent a significant achievement for Staticus, but will also be a milestone in what we hope will be a much longer journey.
The long-term performance of our HUF system has been the subject of much research by the project team. Our project partners SINTEF have outlined some of the challenges, and also detailed how we are working to include Internet of Things (IoT) sensors and use digital twins for effective façade maintenance. The culmination of this work will be creating an AI-driven predictive maintenance model that uses data from these sensors to preemptively manage the façades upkeep, thus extending its working lifetime while reducing maintenance costs.
We are excited to further develop our HUF system, and immensely proud to see it deployed in a project.
The Hybrid Unitized Facade (HUF) system is a part of a project Staticus Care funded by the 2014-2021 Norwegian Financial Mechanism Program “Business Development, Innovation and SMEs” EEA and Norway Grants. The project is being conducted in partnership with Kaunas University of Technology, OsloMet – Oslo Metropolitan University, and SINTEF.